What is Aluminum Extrusion?
Aluminum extrusion transforms aluminum alloy into objects with specific cross-sectional profiles. This process uses a hydraulic press to force the material through a die, shaping it under high pressure. The result is lightweight, durable components suitable for various applications.
In this method, the aluminum billet first heats to approximately 900°F (482°C). Then, it’s pushed through a steel die using a ram or hydraulic press capable of exerting thousands of tons of pressure. This action causes the aluminum to take on the shape of the die’s opening, creating long pieces with uniform cross-sections.
The extruded aluminum cools and hardens quickly after exiting the die. It can then be cut to desired lengths and further treated if necessary. Common post-extrusion treatments include heat treatment and surface finishing such as anodizing or painting.
Extruded aluminum finds use in many industries due to its versatility and excellent properties. For example:
- Automotive Industry: Components like chassis, frames, and engine parts.
- Construction and Architecture: Window frames, curtain walls, and structural materials.
- Electronics: Heat sinks for electronic devices.
- Aerospace: Aircraft components requiring strength without added weight.
Each application benefits from aluminum's malleability combined with its strength-to-weight ratio. The ability to produce complex shapes with tight tolerances makes extrusion vital in modern engineering solutions across industries.
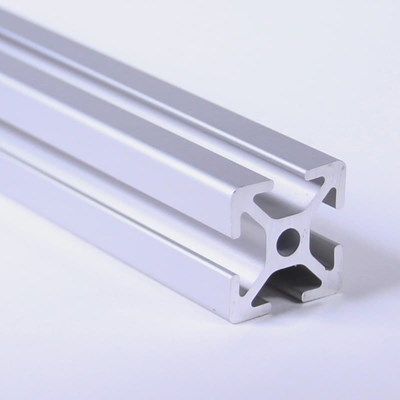
Aluminum Extrusion Basics
Aluminum extrusion involves forcing aluminum alloy through a die to create objects with specific cross-sectional profiles. The process starts by heating an aluminum billet to approximately 900°F (482°C). Once heated, the softened aluminum is pushed through a steel die using a hydraulic press under high pressure.
Key Components
Several components are integral to the extrusion process:
- Die: A steel tool designed to shape the extruded aluminum.
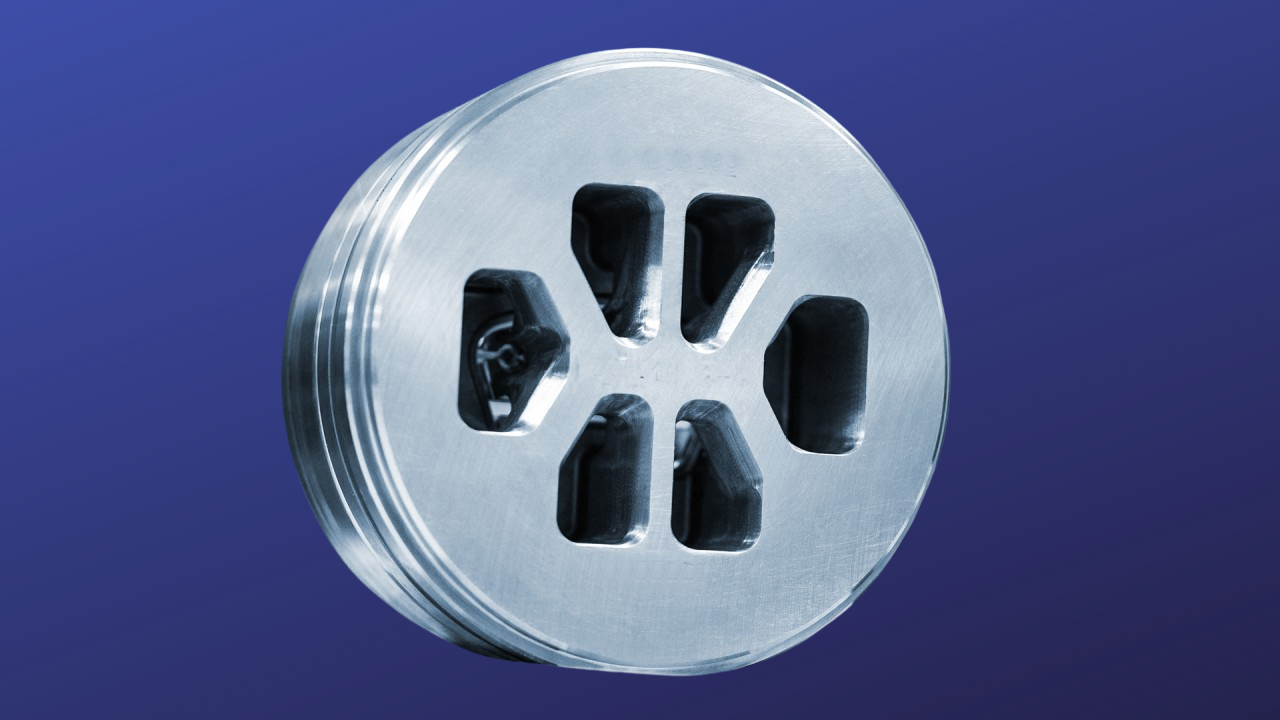
- Billet: A cylindrical piece of aluminum alloy that gets heated and extruded.
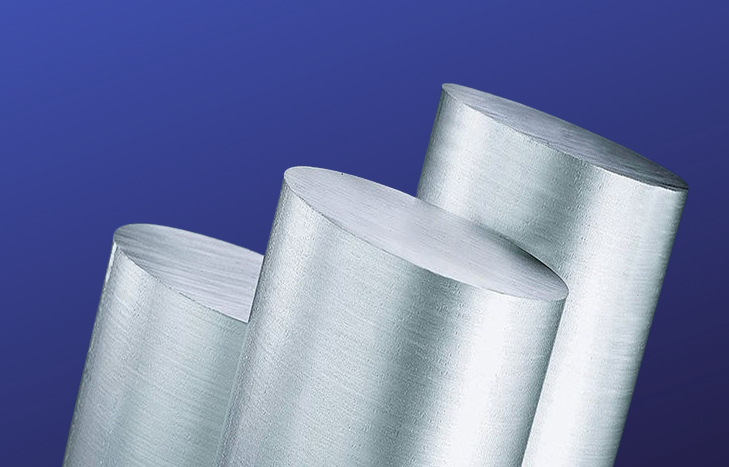
- Hydraulic Press: Machinery used to apply high pressure and push the billet through the die.
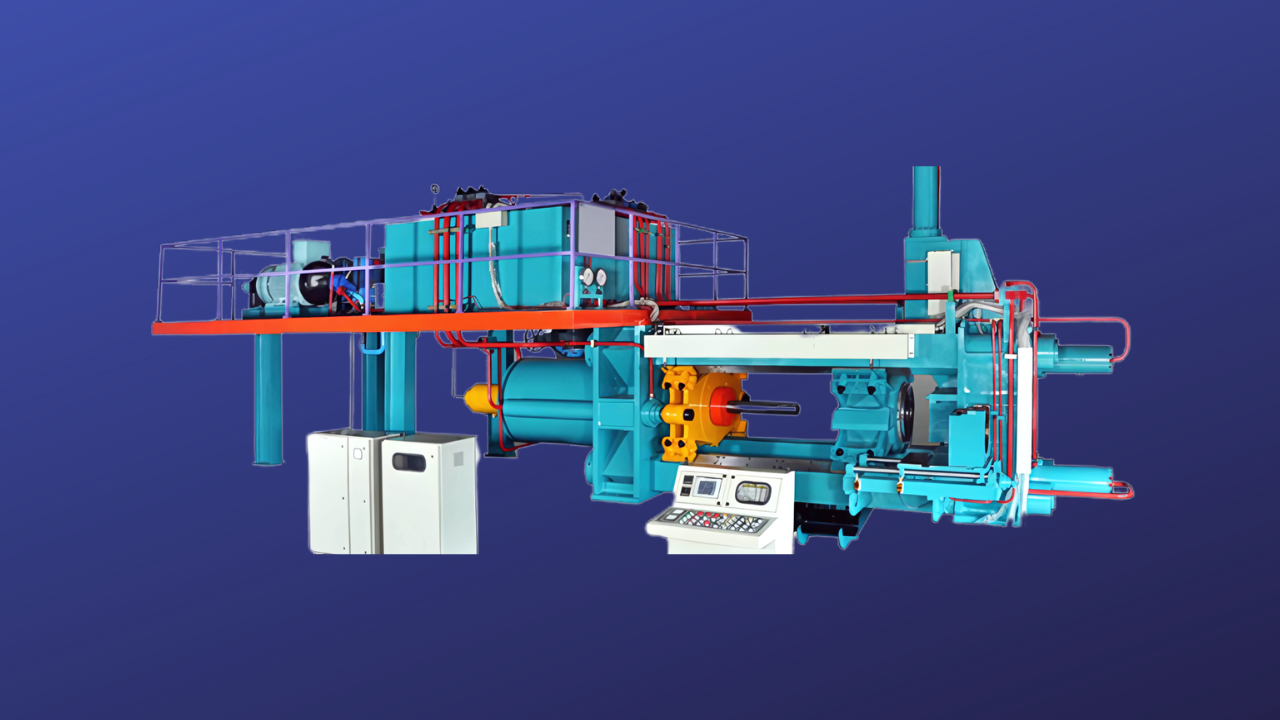
Steps in Aluminum Extrusion
The following steps outline the basic procedure:
- Preheating the Billet: The billet is heated uniformly to around 900°F (482°C), making it malleable.
- Loading into Press Container: The preheated billet is placed into a container within the hydraulic press.
- Extruding Through Die: High-pressure force pushes the billet through the die, shaping it into desired profiles.
- Cooling and Cutting: The extruded product cools down before being cut to required lengths.
Post-Extrusion Treatments
Extruded aluminum often undergoes additional treatments for enhanced properties:
- Heat Treatment: Increases strength and durability.
- Anodizing: Enhances corrosion resistance and surface finish.
- Painting or Powder Coating: Provides aesthetic appeal and extra protection.
Industrial applications depend on these treatments for producing high-performance components.
Factors Affecting Extrusion
Several factors influence the aluminum extrusion process, impacting the quality and efficiency of the final product.
Temperature
Temperature plays a critical role. The billet must reach approximately 900°F (482°C) for optimal malleability. Deviations can lead to defects or inefficient extrusions.
Alloy Composition
Different alloys exhibit varied behaviors during extrusion. Alloys with higher silicon content, like 6063, offer better extrudability compared to those with high copper content.
Die Design
Die design determines the shape and complexity of the extruded profile. Complex designs may require more precise engineering and maintenance to ensure consistent results.
Press Speed
Press speed impacts material flow through the die. Slower speeds produce finer details but take longer. Faster speeds increase production but may compromise detail accuracy.
Lubrication
Lubrication reduces friction between the billet and die, preventing wear and tear while facilitating smoother extrusion processes.
Billet Quality
Billet quality affects overall product integrity. Homogeneous billets free from contaminants yield better structural properties in extruded items.
These factors collectively determine how efficiently an aluminum alloy transforms into desired shapes through extrusion, affecting industries such as automotive, construction, electronics, and aerospace by ensuring reliable performance in applications like car frames, building facades, electronic housings, and aircraft components.
Primary Methods to Shape
1-Direct Extrusion
Direct extrusion involves forcing the aluminum billet through a stationary die using a moving ram. This method is commonly used due to its simplicity and efficiency. The billet moves in the same direction as the ram, making it easier to control the extrusion process.
2-Indirect Extrusion
Indirect extrusion uses a stationary billet while the die moves towards it. This technique reduces friction between the billet and container, resulting in less force required for extrusion. It's beneficial for extruding long sections with uniform properties.
Both methods have their advantages:
- Direct Extrusion: Offers higher production rates, suitable for various profile shapes.
- Indirect Extrusion: Reduces material waste and energy consumption, ideal for precise applications.
Choosing between these methods depends on factors like desired profile complexity, material characteristics, and production efficiency needs.
Temper
Temper is a critical aspect of the aluminum extrusion process. It refers to the mechanical and thermal treatments applied to extruded aluminum to achieve specific properties like strength, hardness, and ductility. Various temper designations indicate different processing methods and resultant characteristics.
Common Temper Designations
- F (As Fabricated): Aluminum in this temper has not undergone any thermal or mechanical treatment after extrusion. It's used when no special property modifications are needed.
- O (Annealed): This temper involves heating aluminum to remove internal stresses, making it soft and ductile for applications requiring extensive forming.
- H (Strain-Hardened): Strain-hardening enhances strength through cold working processes like rolling or stretching without heat treatment.
- T (Thermally Treated): This involves solution heat treatment followed by artificial aging to increase strength and hardness.
Specific T-Temper Subcategories
- T4: Solution heat-treated and naturally aged at room temperature.
- T5: Cooled from an elevated temperature shaping process then artificially aged.
- T6: Solution heat-treated followed by artificial aging for maximum strength.
- T7: Solution heat-treated then overaged/stabilized for dimensional stability under high temperatures.
Choosing the right temper ensures optimal performance based on application-specific requirements, enhancing efficiency and longevity in products utilizing aluminum extrusions. Take the first step towards enhanced performance and efficiency. Contact our experts today to discuss your Aluminum Extrusion needs.