Qu'est-ce que l'extrusion d'aluminium ?
L'extrusion de l'aluminium transforme l'alliage d'aluminium en objets présentant des profils de section transversale spécifiques. Ce procédé utilise une presse hydraulique pour forcer le matériau à travers une filière, en le façonnant sous haute pression. Il en résulte des composants légers et durables, adaptés à diverses applications.
Dans cette méthode, la billette d'aluminium est d'abord chauffée à environ 900°F (482°C). Elle est ensuite poussée à travers une matrice en acier à l'aide d'un vérin ou d'une presse hydraulique capable d'exercer des milliers de tonnes de pression. L'aluminium prend ainsi la forme de l'ouverture de la filière, créant de longues pièces de section uniforme.
L'aluminium extrudé refroidit et durcit rapidement après sa sortie de la filière. Il peut ensuite être coupé à la longueur souhaitée et subir d'autres traitements si nécessaire. Les traitements post-extrusion les plus courants sont le traitement thermique et la finition de surface, comme l'anodisation ou la peinture.
L'aluminium extrudé est utilisé dans de nombreuses industries en raison de sa polyvalence et de ses excellentes propriétés. En voici quelques exemples :
•Industrie automobile : Composants tels que châssis, cadres et pièces de moteur.
•Construction et architecture : Cadres de fenêtres, murs-rideaux et matériaux structurels.
•Électronique : Dissipateurs de chaleur pour appareils électroniques.
•Aérospatiale : Composants aéronautiques nécessitant une résistance sans poids supplémentaire.
Chaque application bénéficie de la malléabilité de l'aluminium et de son rapport poids/résistance. La capacité à produire des formes complexes avec des tolérances serrées rend l'extrusion vitale pour les solutions d'ingénierie modernes dans tous les secteurs.
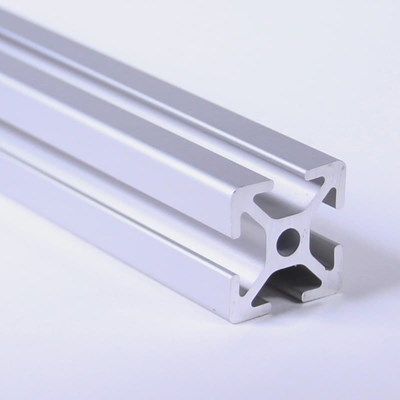
Principes de base de l'extrusion d'aluminium
L'extrusion de l'aluminium consiste à forcer un alliage d'aluminium à travers une filière pour créer des objets ayant des profils de section transversale spécifiques. Le processus commence par le chauffage d'une billette d'aluminium à environ 900°F (482°C). Une fois chauffé, l'aluminium ramolli est poussé à travers une filière en acier à l'aide d'une presse hydraulique sous haute pression.
Composants clés
Plusieurs composants font partie intégrante du processus d'extrusion:
Filière : outil en acier conçu pour façonner l'aluminium extrudé.
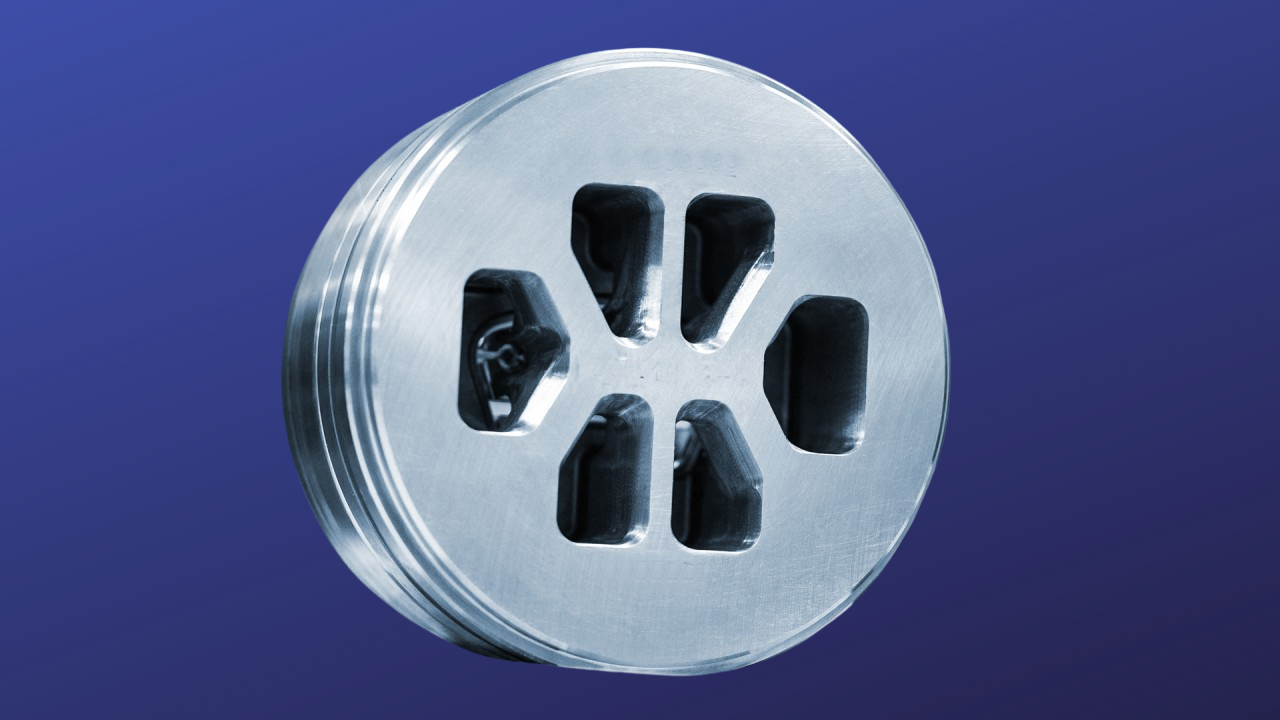
Billet : Une pièce cylindrique en alliage d'aluminium qui est chauffée et extrudée.
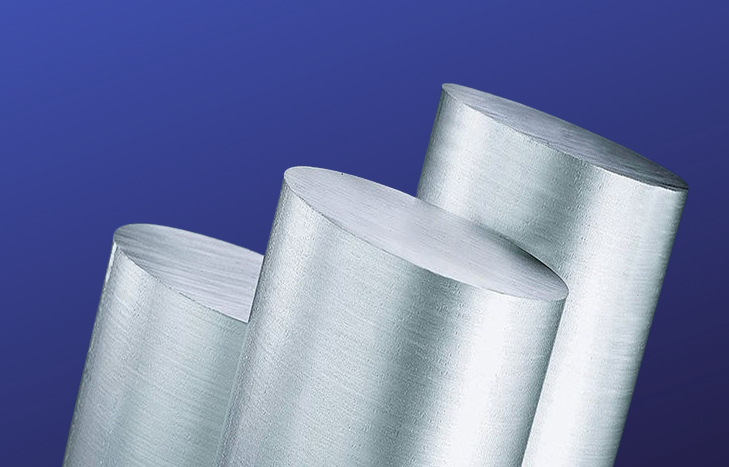
Presse hydraulique : Machine utilisée pour appliquer une pression élevée et pousser la billette à travers la matrice.
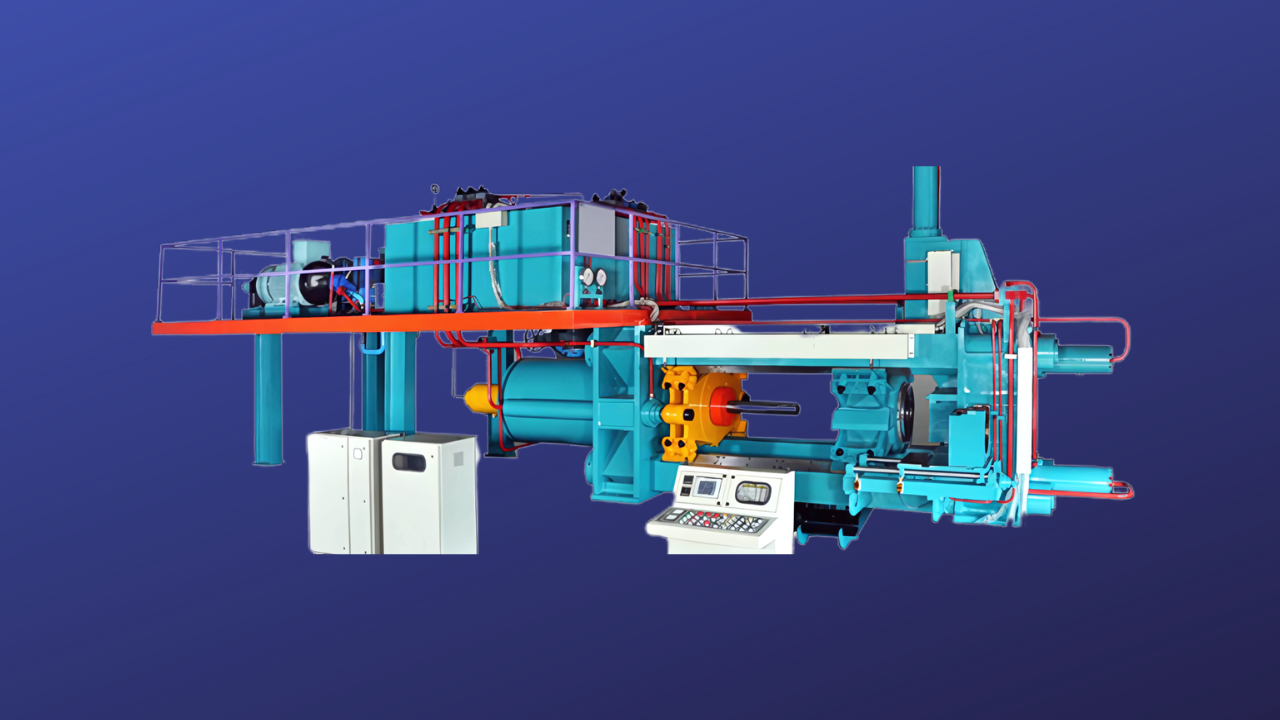
Les étapes de l'extrusion d'aluminium
Les étapes suivantes décrivent la procédure de base :
- Préchauffage de la billette: La billette est chauffée uniformément à environ 900°F (482°C), ce qui la rend malléable.
- Chargement dans le conteneur de la presse: La billette préchauffée est placée dans un conteneur à l'intérieur de la presse hydraulique.
- Extrusion à travers la filière: une force à haute pression pousse la billette à travers la filière, la façonnant selon les profils souhaités.
- Refroidissement et découpe: Le produit extrudé refroidit avant d'être coupé à la longueur voulue.
Traitements de post-extrusion
L'aluminium extrudé subit souvent des traitements supplémentaires pour améliorer ses propriétés :
- Traitement thermique: Augmente la résistance et la durabilité.
- Anodisation: Améliore la résistance à la corrosion et la finition de la surface.
- Peinture ou revêtement par poudre: Apporte un attrait esthétique et une protection supplémentaire.
Les applications industrielles dépendent de ces traitements pour produire des composants de haute performance.
Facteurs affectant l'extrusion
Plusieurs facteurs influencent le processus d'extrusion de l'aluminium et ont un impact sur la qualité et l'efficacité du produit final.
Température
La température joue un rôle essentiel. La billette doit atteindre environ 482°C (900°F) pour une malléabilité optimale. Des écarts peuvent entraîner des défauts ou des extrusions inefficaces.
Composition de l'alliage
Les différents alliages présentent des comportements variés au cours de l'extrusion. Les alliages à forte teneur en silicium, comme le 6063, offrent une meilleure extrudabilité que ceux à forte teneur en cuivre.
Conception de la filière
La conception de la filière détermine la forme et la complexité du profilé extrudé. Les conceptions complexes peuvent nécessiter une ingénierie et une maintenance plus précises pour garantir des résultats constants.
Vitesse de la presse
La vitesse de la presse a un impact sur le flux du matériau à travers la matrice. Les vitesses plus lentes produisent des détails plus fins mais prennent plus de temps. Les vitesses plus rapides augmentent la production mais peuvent compromettre la précision des détails.
Lubrification
La lubrification réduit la friction entre le billette et la filière, évitant ainsi l'usure et facilitant des processus d'extrusion plus fluides.
Qualité Billet
La qualité des billettes affecte l'intégrité globale du produit. Des billettes homogènes et exemptes de contaminants confèrent de meilleures propriétés structurelles aux produits extrudés.
Ces facteurs déterminent collectivement l'efficacité avec laquelle un alliage d'aluminium se transforme en formes souhaitées par extrusion, ce qui affecte des industries telles que l'automobile, la construction, l'électronique et l'aérospatiale en garantissant des performances fiables dans des applications telles que les châssis de voitures, les façades de bâtiments, les boîtiers électroniques et les composants d'aéronefs.
Méthodes primaires de mise en forme
1-Extrusion directe
L'extrusion directe consiste à forcer la billette d'aluminium à travers une filière stationnaire à l'aide d'un coulisseau mobile. Cette méthode est couramment utilisée en raison de sa simplicité et de son efficacité. La billette se déplace dans la même direction que le coulisseau, ce qui facilite le contrôle du processus d'extrusion.
2-Extrusion indirecte
L'extrusion indirecte utilise un lopin stationnaire tandis que la filière se déplace vers lui. Cette technique réduit la friction entre la billette et le récipient, ce qui diminue la force nécessaire à l'extrusion. Elle permet d'extruder de longues sections aux propriétés uniformes.
Les deux méthodes ont leurs avantages :
- Extrusion directe : Offre des taux de production plus élevés et convient à diverses formes de profilés.
- Extrusion indirecte : Réduit les pertes de matériaux et la consommation d'énergie, idéal pour les applications précises.
Le choix entre ces méthodes dépend de facteurs tels que la complexité du profil souhaité, les caractéristiques du matériau et les besoins d'efficacité de la production.
Tempérament
Le revenu est un aspect essentiel du processus d'extrusion de l'aluminium. Il s'agit des traitements mécaniques et thermiques appliqués à l'aluminium extrudé pour obtenir des propriétés spécifiques telles que la résistance, la dureté et la ductilité. Les différentes désignations d'état indiquent les différentes méthodes de traitement et les caractéristiques qui en résultent.
Désignations courantes des températures
- F (tel que fabriqué) : L'aluminium de cette nuance n'a subi aucun traitement thermique ou mécanique après l'extrusion. Il est utilisé lorsqu'aucune modification particulière des propriétés n'est nécessaire.
- O (recuit) : Cette trempe consiste à chauffer l'aluminium pour éliminer les tensions internes, ce qui le rend souple et ductile pour les applications nécessitant un formage important.
- H (Strain-Hardened) : L'écrouissage renforce la résistance par des procédés d'usinage à froid tels que le laminage ou l'étirement sans traitement thermique.
- T (Thermally Treated) : Il s'agit d'un traitement thermique en solution suivi d'un vieillissement artificiel pour augmenter la résistance et la dureté.
Sous-catégories spécifiques de T-Temper
- T4 : Traitement thermique de mise en solution et vieillissement naturel à température ambiante.
- T5 : Refroidissement après un processus de mise en forme à température élevée, puis vieillissement artificiel.
- T6 : Traitement thermique de mise en solution suivi d'un vieillissement artificiel pour une résistance maximale.
- T7 : Traitement thermique de mise en solution suivi d'un sur-vieillissement/stabilisation pour assurer la stabilité dimensionnelle à des températures élevées.
Le choix de la bonne trempe garantit des performances optimales en fonction des exigences spécifiques de l'application, améliorant ainsi l'efficacité et la longévité des produits utilisant des extrusions d'aluminium. Faites le premier pas vers une performance et une efficacité accrues. Contactez nos experts dès aujourd'hui pour discuter de vos besoins en matière d'extrusion d'aluminium.