Search blog posts
Search blog posts
155 articles
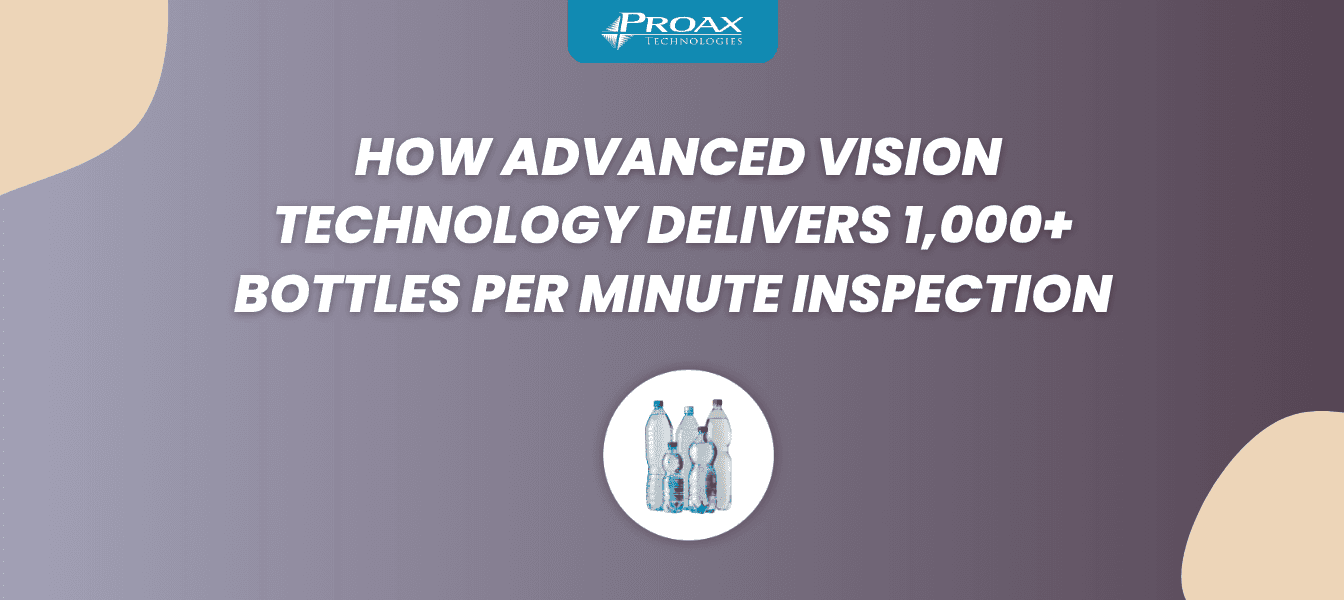
Food and BeverageRevolutionizing Bottled Water Quality Control: How Advanced Vision Technology Delivers 1,000+ Bottles Per Minute Inspection
Jun 30, 2025|
Picture this: your bottling line is running at full speed, but you're constantly worried about defective products slipping through inspection. Misaligned caps damage equipment downstream, contamination issues create costly recalls, and your brand reputation hangs in the balance with every bottle that leaves the facility.
This scenario recently played out for a major North American bottled water manufacturer, and the solution they implemented showcases how advanced machine vision technology can transform quality control while maintaining production speeds exceeding 1,000 bottles per minute.
The Industry Challenge: Speed vs. Quality in Beverage Production
The beverage industry faces unique quality control challenges that traditional inspection methods struggle to address effectively. This particular manufacturer was experiencing significant issues with their existing bottle inspection system:
* Inadequate cap detection: Bottle caps with small trapezoidal surfaces couldn't be properly evaluated
* Critical blind spots: Two-camera systems missed tilted caps in certain orientations
* Equipment damage: Misaligned caps were damaging downstream machinery
* Quality escapes: Defective products reaching consumers and threatening brand integrity
These challenges are common across the beverage industry, where high-speed production lines demand both speed and precision.
Understanding Beverage Industry Quality Requirements
Cap placement and seal integrity are fundamental to beverage quality and safety. Common issues that can compromise production include:
* Plastic burrs interfering with proper cap placement
* Misaligned or upside-down caps during feeding
* Cap feeder jams and equipment malfunctions
* Malformed bottle necks affecting seal quality
* Improper threading causing loose or over-tightened caps
* Production changeovers introducing tolerance variations
When these defects go undetected, the consequences extend throughout the supply chain, affecting equipment reliability, product safety, and brand reputation.
The Technology Solution: High-Speed Vision Inspection
As an authorized Omron distributor, Proax recognizes the power of advanced vision sensors and systems in addressing these critical beverage industry challenges. The manufacturer's success story showcases what's possible with the right technology approach.
How FH Vision Systems Achieve 1,000+ Bottles Per Minute Inspection
The Omron FH vision system delivers exceptional performance for high-speed beverage applications through several key capabilities:
High-Speed Processing Power
* High-speed CMOS cameras capture clear images at production speeds
* Simultaneous processing of up to four images ensures comprehensive inspection
* Real-time decision making keeps pace with fast production lines
Complete Quality Coverage
* Liquid-level verification ensures proper fill volumes
* Cap placement and integrity monitoring prevents seal failures
* Tamper-band inspection confirms security features
* Label positioning and quality verification
Advanced Code Reading Capabilities The system excels at critical traceability requirements:
* Date code, lot code, and factory code verification
* Comparison against system time and location data
* Reliable reading of both ink-printed and laser-marked codes
* Proven performance on curved, compressed, elongated, or damaged codes
Strategic Camera Positioning for Complete Coverage
The successful implementation utilized strategic camera placement to eliminate blind spots:
* Two cameras positioned 90 degrees apart
* 45-degree angle to bottle flow for optimal visibility
* Four inspection points at 90-degree intervals around each cap
* Complete 360-degree monitoring of critical quality parameters
Measurable Results in Beverage Production
The implementation delivered significant operational improvements:
Quality Achievements
* 100% inspection coverage eliminating quality escapes
* Zero blind spots ensuring comprehensive defect detection
* Automated verification removing manual inspection requirements
* Consistent quality standards across all production shifts
Operational Benefits
* Reduced product waste through early defect detection
* Equipment protection preventing downstream damage
* Eliminated contamination from seal integrity issues
* Decreased customer complaints and returns
Business Impact
The success was so significant that the manufacturer expanded the solution to seven additional facilities nationwide, demonstrating the scalability and reliability of the technology.
Why Choose the Right Technology Partner
At Proax, we understand the unique challenges facing beverage manufacturers. Our expertise in vision sensors and systems combined with our status as an authorized Omron partner ensures access to cutting-edge technology and comprehensive support for both end users and system integrators.
Our "Boots On the Ground" Approach
We're currently running our "Boots On the Ground" campaign, where we come to your facility for free to solve your production bottlenecks. This proven process identifies and solves challenges in a single visit:
1. Pre-Visit Preparation
* We gather information about your facility and specific needs to prepare for an effective visit
2. On-Site Assessment
* Our sales and technical teams along with Omron specialists conduct a thorough assessment
3. Customized Solutions
* We develop tailored solutions with our product offerings and in-house technical capabilities based on our assessment and your specific requirements
Supporting Your Success
* Application analysis: Understanding specific production requirements
* Technical consultation: Providing expert guidance on optimal solutions
* Product availability: Ensuring reliable supply and support
* Performance optimization: Helping maximize throughput and quality results
Technology Advantages for Beverage Applications
The Omron FH Series vision system offers several advantages specifically beneficial for beverage production:
Scalability and Flexibility
* Support for up to 16 cameras for complex multi-station inspection
* Compatibility with various GigE Vision cameras
* Adaptable to different bottle sizes and production configurations
Real-Time Intelligence
* Manufacturing process monitoring and statistical process control
* Immediate feedback for process adjustments
* Data logging for quality compliance and traceability
User-Friendly Operation
* Menu-driven software simplifies setup and operation
* PC-based integration for familiar interface
* Comprehensive diagnostic capabilities
Applications Beyond Basic Inspection
Modern vision systems can address multiple beverage industry requirements simultaneously:
* Product identification: Verify correct products on specific lines
* Label inspection: Ensure proper placement, print quality, and compliance
* Date and lot coding: Critical for traceability and recall management
* Fill level consistency: Maintain consumer satisfaction and regulatory compliance
* Packaging integrity: Detect damage or contamination before shipping
Ready to explore vision system solutions for your applications? Contact us today to discuss your requirements and discover how proven inspection technology can deliver the reliability and performance your projects demand.
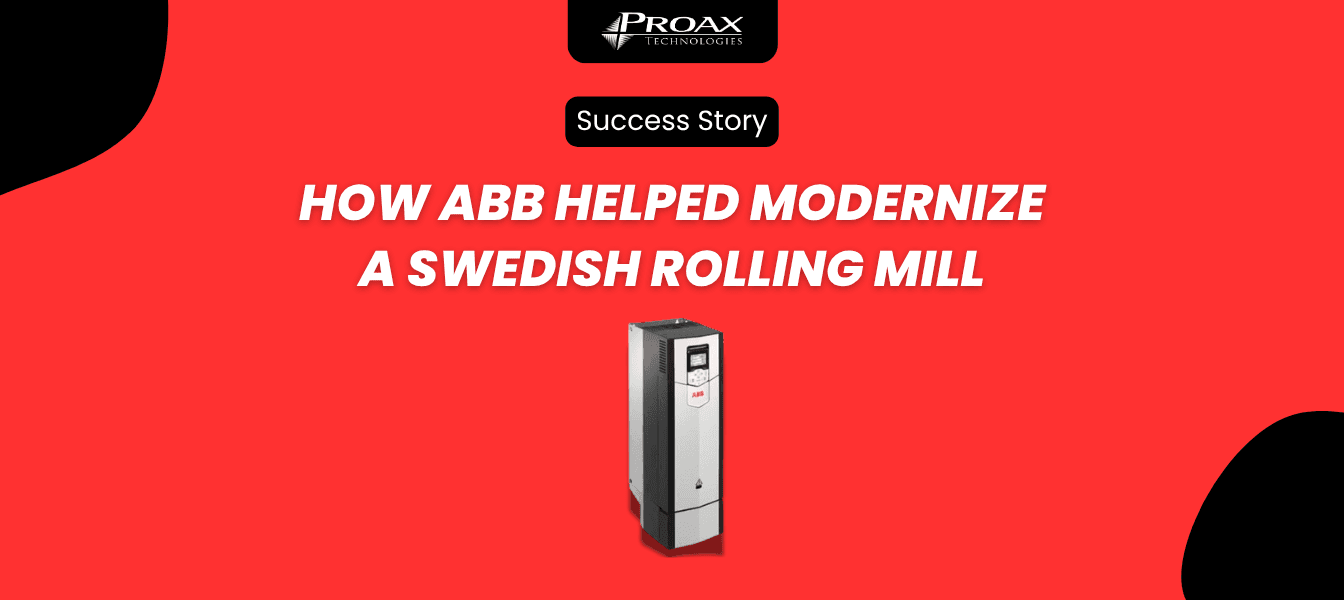
Success StoriesFrom Outdated to Optimized: How ABB Helped Modernize a Swedish Rolling Mill and How Proax Can Help You in Canada
Jun 27, 2025|
Kanthal AB, a leading steel manufacturer in Sweden, recently faced a critical challenge. Their rolling mill in Hallstahammar had relied on a DC motor and drive system installed more than 70 years ago. Spare parts were scarce, downtime risks were increasing, and system efficiency was falling behind modern standards.
ABB stepped in with a complete modernization plan. While this success story took place overseas, the same level of transformation is available here in Canada — through Proax, an ABB Value Provider and authorized distributor.
The Kanthal Upgrade: A Proven Success
In the summer of 2021, ABB replaced Kanthal’s aging DC drive system with a fully integrated AC solution, built around the highly efficient ACS880 drive series. The upgrade included:
* A new AC motor and ACS880 drive system
* A 70-ton gearbox, transformer, and control system
* Full electrical and mechanical installation
* On-site commissioning, testing, and foundation work
The results were significant:
* Energy efficiency improved dramatically, with harmonic distortion dropping from 30% to 3–4%
* Reliability increased and unplanned stoppages decreased
* Operators gained greater process visibility and control via real-time monitoring
* Maintenance costs dropped thanks to newer technology and simplified upkeep
Bringing the Same Expertise to Canadian Manufacturers
At Proax, we bring ABB’s global innovation to Canadian manufacturing environments. As an ABB Value Provider and authorized distributor, we don’t just supply products. We deliver complete solutions.
Whether you're operating a metals facility, a packaging plant, or a food and beverage line, our local teams help you modernize with:
* Technical consultation and design expertise
* On-site support throughout deployment and after-sales service
* Hands-on training to help your team operate and maintain systems confidently
National Support with Local Commitment
Our in-house engineering team is equipped to assist with everything from drive sizing and selection to integration, programming, and commissioning. We understand your application challenges and tailor ABB solutions for long-term reliability and performance.
With our campaign named Boots on the Ground, our team members and manufacturer reps are currently touring facilities across Canada — offering free automation consultations directly on-site. It’s part of our commitment to stay close to our customers and offer proactive support where it matters most.
Explore the Right Solutions
Ready to modernize like Kanthal did? We offer the same ABB drives and expertise to Canadian facilities:
* ABB ACS880 Single Drives
* Explore All Drive Solutions
Reference
ABB Modernization Drives Efficiency at Kanthal’s Rolling Mill in Sweden
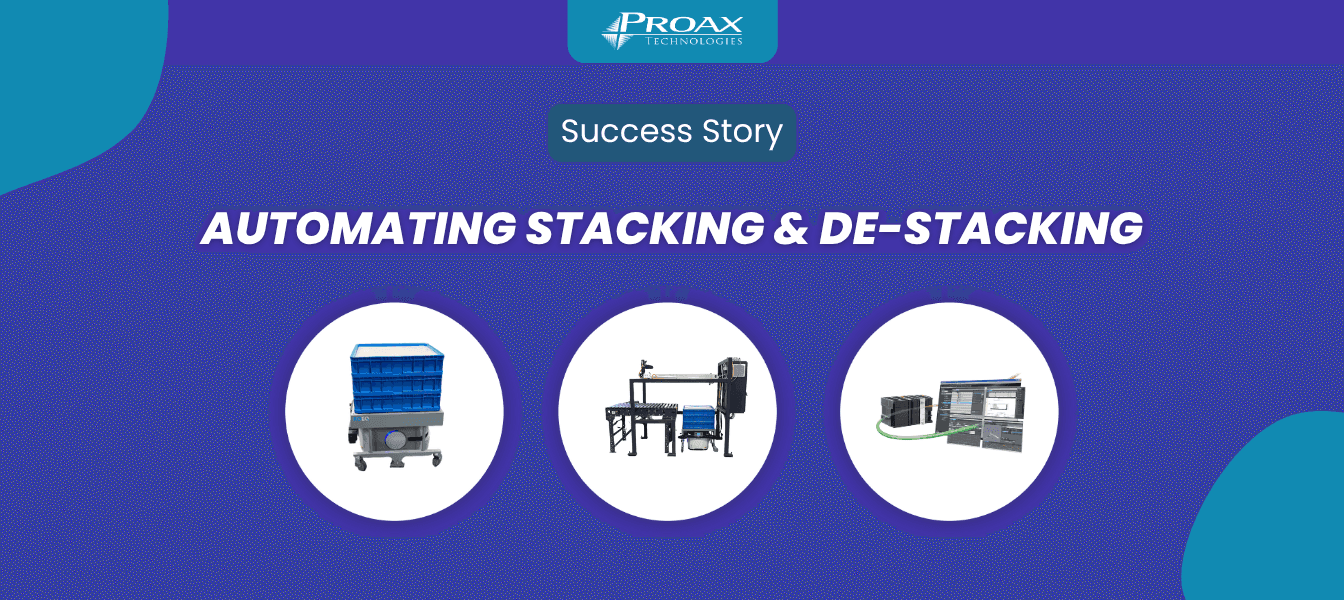
Success StoriesSuccess Story: Automating Stacking & De-Stacking with Omron Sysmac
Jun 26, 2025|
A leading manufacturer in the precision tooling and fabrication industry recently transformed its operations with a fully automated stacker and de-stacker solution powered by Omron’s Sysmac platform. Facing challenges related to manual handling and space constraints, the manufacturer set out to modernize its material flow—achieving measurable gains in safety, speed, and Just-In-Time (JIT) logistics.
?
Reduced Labor Costs
?️
Improved Safety
⚙️
Increased Efficiency
The Challenge
Manual stacking was a bottleneck. Workers were regularly exposed to ergonomic strain, floor space was being used inefficiently, and staging operations introduced variability that complicated production schedules.
Key issues included:
* High injury risk and rising labor costs from repetitive manual stacking
* Throughput limitations and inconsistent handling
* Inefficient staging consuming critical warehouse real estate
* Pressure to meet tight JIT delivery timelines
The Solution
With support of Omron’s Sysmac platform, the manufacturer deployed an advanced automated stacker and de-stacker system.
This solution featured:
* High-speed EtherCAT® communication for real-time control
* Fully integrated conveyor and handling systems designed to manage a wide range of tote and pallet sizes
* Seamless integration into the customer’s production line with minimal disruption
The result? An intelligent system that stacks and de-stacks reliably, optimizes space, reduces manual labor, and ensures consistent operation across shifts. You can also check out our promotion the power of one sysmac solutions.
The Results
The benefits were immediate and impactful:
* Reduced labor costs and improved worker safety
* Increased process efficiency and production consistency
* Optimized material flow, supporting reliable JIT logistics
With enhanced operational control, the manufacturer now meets delivery targets with greater confidence while freeing up valuable floor space and human resources for higher-value tasks.
Boots on the Ground
As a trusted Omron distributor, Proax played a key role in this deployment—backed by our in-house engineering team and deep experience in automation integration.
What sets us apart?
* Technical consultation and design expertise
* On-site support throughout deployment and after-sales service
* Hands-on training to help your team operate and maintain your systems confidently — Explore our trainings
* With our campaign named boots on the ground, our team members and manufacturer reps are now touring facilities across Canada, bringing free automation consultations directly to manufacturers like you.
We don’t just sell parts. We bring full solutions to life, tailored to your plant’s needs. Ready to take the next step in automation? Let’s talk. Connect with our team to bring industrial automation to your facility.
Related Categories & Series
Box PC with Sysmac-PLC-MCE
Panel PC with Sysmac-PLC-MCE
NX1P Machine Automation Controller
Machine Automation Controllers
1S Drives EtherCAT Sysmac General-Purpose Servo
NJ5 Series Machine Automation Controller

PneumaticsSMC MXS vs. MXQ Precision Slide Tables: A Comprehensive Comparison
May 28, 2025|
SMC’s MXS and MXQ series are among the most popular precision slide tables used in industrial automation, prized for their high accuracy, rigidity, and versatility. Both series are designed for precise linear motion in compact spaces, but they differ in guide technology and certain performance characteristics. This comparison will help you understand their differences, strengths, and the industries where they excel.
Key Features Overview
FeatureSMC MXS SeriesSMC MXQ SeriesGuide TypeCross roller bearingsRecirculating ball bearingsBore Sizes (mm)6, 8, 12, 16, 20, 256, 8, 12, 16, 20, 25Stroke Range (mm)10–150 (varies by bore size)10–150 (varies by bore size)Positioning AccuracyHigh (±0.05 mm repeatability)Very high (±0.05 mm repeatability)RigidityHigh (due to cross roller guide)Higher (wider guide pitch, increased rigidity)OptionsStroke adjuster, shock absorber, end lock, bufferStroke adjuster, shock absorber, end lock, bufferMounting3 directions (side, axial, vertical)3 directions (side, axial, vertical)Auto Switch CapabilityYesYesRoHS CompliantYesYesFood Grade Grease OptionYesYes
Technical Comparison
Guide Mechanism
* MXS uses cross roller bearings, providing smooth movement with minimal play and high precision, making it ideal for applications where rigidity and accuracy are paramount.
* MXQ employs recirculating ball bearings, which offer even greater rigidity, improved load resistance (up to three times higher than MXS), and superior parallelism and perpendicularity.
Load and Rigidity
* The MXQ’s design, with a wider guide pitch and hardened stainless steel rails, allows it to handle higher moments and heavier loads than the MXS, making it more suitable for demanding industrial environments
Stroke and Mounting
* Both series offer similar stroke ranges and flexible mounting options, including side, axial, and vertical mounting, allowing integration into various machine layouts
Functional Options
* Both MXS and MXQ can be equipped with stroke adjusters (rubber, metal, or shock absorber), end lock (prevents table drop in case of air loss), and buffer mechanisms for smooth stopping
* Auto switch capability is standard, supporting process monitoring and automation integration
Specialized Versions
* The MXQ offers a high-durability (XC4) variant for dusty environments, with up to four times the standard model’s durability, suitable for industries processing powders or fine particulates
Application Examples
Industries and Typical Uses
IndustryApplication ExampleSeries PreferenceElectronics/AssemblyPrecision assembly, pick-and-place, PCB handlingMXS or MXQAutomotiveSmall part transfer, inspection, fixture positioningMXQ (higher load)PackagingSorting, labeling, light material handlingMXS or MXQMedical Device ManufacturingMicro-assembly, small part handlingMXS (precision)SemiconductorWafer handling, clean room automationMXQ (clean room, dust)Food & BeveragePackaging, sorting (with food grade grease option)MXS or MXQRobotics/AutomationEnd-of-arm tooling, precise motion controlMXQ
Why Choose MXS?
* Best for applications demanding high precision and smooth movement with moderate loads, such as electronics assembly or light pick-and-place tasks.
MXS Digital Catalog
Why Choose MXQ?
* Ideal for applications requiring higher rigidity, load capacity, or operation in dusty environments, such as automotive component transfer or industrial automation in harsh conditions.
MXQ Digital Catalog
Summary Table: MXS vs. MXQ
Feature/NeedBest ChoiceReasonHighest rigidity & loadMXQRecirculating bearings, wide guide pitchBest for precisionBothBoth offer ±0.05 mm repeatabilitySmoothest movementMXSCross roller bearings minimize playDusty/harsh environmentsMXQXC4 variant for powder/dust resistanceClean room compatibilityMXQEnhanced durability in clean environmentsCompact/lightweightBothBoth designed for compact spacesExtensive optionsBothStroke adjusters, end lock, buffer, etc.
MXQ & MXS Air Slide Tables Datasheet
Conclusion
Both the SMC MXS and MXQ series are highly capable precision slide tables, but your choice should be guided by the specific requirements of your application:
* Choose MXS for high-precision, smooth, moderate-load tasks in compact assemblies.
* Choose MXQ for higher rigidity, greater load capacity, or environments with dust or particulates, and when the highest repeatability and mounting flexibility are needed.
Need help choosing the right SMC slide table for your application? Contact Proax today — our automation experts are here to help.
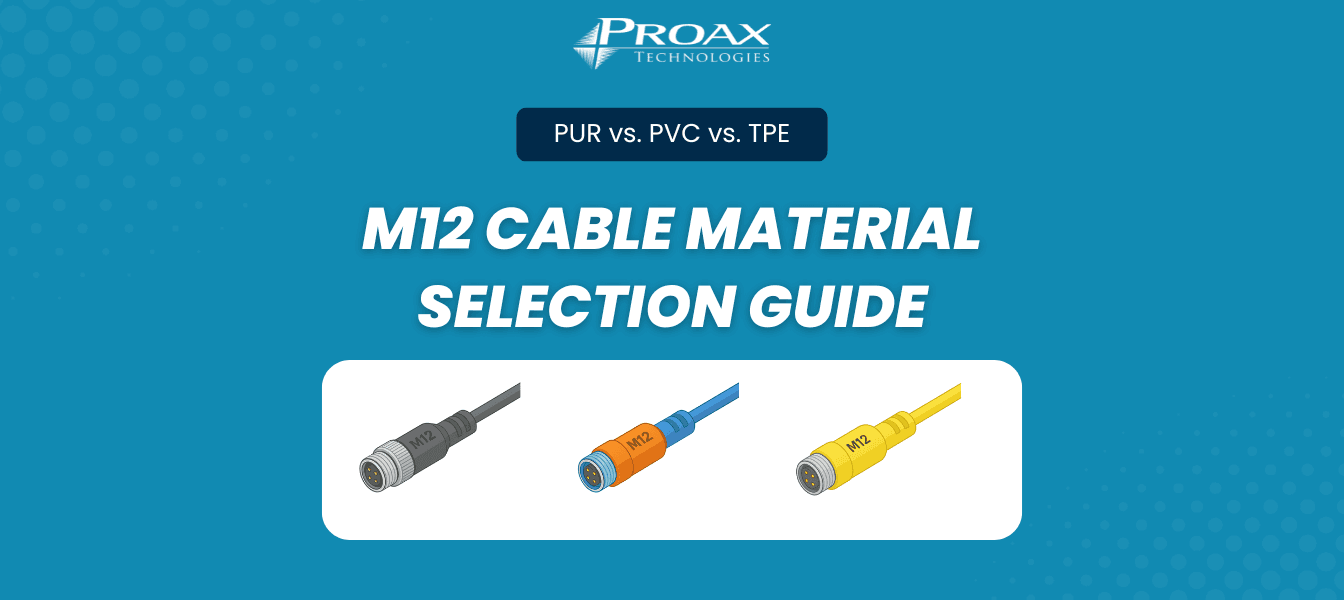
AutomationM12 Cable Material Selection Guide: PUR vs. PVC vs. TPE
May 2, 2025|
M12 Cables have become the industry standard for sensor/actuator connectivity in industrial automation environments. When selecting the right M12 cable for your application, the jacket material is one of the most critical factors that will determine performance, durability, and reliability. This guide compares the three most common M12 cable jacket materials: PUR (Polyurethane), PVC (Polyvinyl Chloride), and TPE (Thermoplastic Elastomer).
Why Material Selection Matters
The right cable jacket material can mean the difference between a reliable connection that lasts for years and frequent cable failures resulting in costly downtime. In fact, according to industry research, up to 70% of field failures in industrial networks are related to cabling issues. By understanding the properties of different materials and making informed selections, you can significantly improve your system's reliability.
Quick Comparison: PUR vs. PVC vs. TPE
Property
PVC
PUR
TPE
FlexibilityModerateHighVery High
Abrasion ResistanceGoodExcellentGood
Chemical ResistanceGood (acids/alkalis)Excellent (oils/chemicals)Excellent
Oil ResistanceModerateExcellentExcellent
UV/Weather ResistanceModerateExcellentExcellent
Temperature Range (°C)-25 to 70-40 to 80-50 to 125
Flame RetardancyGoodGoodExcellent
Flex LifeModerateHighVery High
Environmental ImpactContains halogensHalogen-free, recyclableNon-toxic, recyclable
Relative CostLowModerate to HighHigh
← Scroll horizontally to view more →
PVC (Polyvinyl Chloride)
Best for: General-purpose, static, and cost-sensitive applications
Advantages:
* Economical solution for basic industrial applications
* Good resistance to common cleaning chemicals and moisture
* Rigid sheathing provides protection in washdown environments
* Ideal for fixed installations with minimal movement
Limitations:
* Less flexible than alternatives, especially in cold temperatures
* Lower resistance to oils and abrasion compared to PUR or TPE
* Contains halogens that can release toxic fumes when burned
Typical Applications:
* General factory automation
* Fixed sensor installations
* Indoor control panels
* Budget-conscious projects
Phoenix Contact PVC M12 Cables
Part Number
Cable Length
Connector Type
Connector Orientation
Sheath Material
1415675
1.5 m
Female
Straight
PVC, black RAL 9005
1544976
1.5 m
Female
Straight
PVC, black RAL 9005
1693539
1.5 m
Female
Angled
PVC, black RAL 9005
1446333
10 m
Female
Straight
PVC, black RAL 9005
1415727
1.5 m
Female
Straight
PVC, black RAL 9005
1414452
10 m
Female
Straight
PVC, black RAL 9005
1554872
1.5 m
Female
Straight
PVC, black RAL 9005
← Scroll horizontally to view more →
PVC M12 Cable Features
All Phoenix Contact PVC M12 cables feature:
* Black RAL 9005 PVC sheath
* A-coded M12 connectors
* Available in both straight and angled orientations
* Multiple length options including 1.5m and 10m
* Standard protection rating of IP65/IP67
* Suitable for applications where flexibility and chemical resistance requirements are moderate
* Economical choice for standard industrial environments
* Operating temperature range: -25°C to 70°C
PUR (Polyurethane)
Best for: Dynamic, abrasive, oily, and outdoor environments
Advantages:
* Outstanding flexibility with small bend radius, perfect for M12 Cables in robotic applications
* Superior resistance to abrasion, tearing, oils, and chemicals
* Excellent weather and UV resistance for outdoor installations
* Halogen-free composition for environmentally conscious applications
Limitations:
* Higher cost compared to PVC options
* Slightly lower heat resistance than some specialized materials
Typical Applications:
* Robotic arm connections
* Machine tools with exposure to cutting fluids
* Outdoor installations
* Mobile equipment
* Applications with continuous movement
Phoenix Contact PUR Halogen-Free M12 Cables
Browse some of our Phoenix Contact PUR halogen-free M12 cables, designed for maximum durability and reliability in demanding industrial environments.
Part Number
Positions
Cable Length
Connector Type
166812445MStraight Female
1683002410MStraight Female
166984855MStraight Female
1683374510MStraight Female
152036985MStraight Female
1520372810MStraight Female
166824745MAngled Female
1681389410MAngled Female
166987755MAngled Female
1694541510MAngled Female
152264285MAngled Female
1522655810MAngled Female
← Scroll horizontally to view more →
All cables feature:
* 100% electrically tested reliability
* PUR halogen-free construction for industrial durability
* Next-day shipping on in-stock items
* Full compatibility with industry-standard M12 connectors
Key Benefits of Our PUR Halogen-Free M12 Cables
* Extended Lifespan: Highly resistant to abrasion, chemicals, oils, and UV radiation
* Operational Versatility: Maintains flexibility in temperatures from -40°C to 80°C
* Environmental Responsibility: Halogen-free composition eliminates toxic emissions during fires
* Cost Efficiency: Reduced replacement frequency and downtime compared to standard cables
* Universal Compatibility: Works seamlessly with all major industrial automation systems
TPE (Thermoplastic Elastomer)
Best for: High-flex, extreme temperature, and environmentally sensitive applications
Advantages:
* Exceptional flexibility with outstanding flex life (up to 10 million cycles)
* Superior performance in extreme cold environments (down to -50°C)
* Excellent resistance to UV radiation, ozone, chemicals, and flame
* Non-toxic formula ideal for food and pharmaceutical applications
Limitations:
* Premium price point
* May be over-specified for basic applications
Typical Applications:
* Continuous flexing applications
* Cold storage and freezer environments
* Food and beverage processing
* Pharmaceutical manufacturing
* Applications requiring extended temperature ranges
* High-pressure washdown areas requiring IP69K-rated cordsets
Conclusion
Selecting the right M12 cable jacket material ensures your installation meets performance, durability, and safety requirements:
* PVC is best for static, indoor, and budget-conscious applications where standard cables are appropriate
* PUR excels in harsh, dynamic, and oily environments requiring premium cables for reliability
* TPE is unmatched for flexibility, cold resistance, and eco-friendliness, especially in IP69K applications
Need help choosing the right M12 cable for your application?
Contact us today — our automation specialists are here to guide you toward the perfect solution for your environment, budget, and performance needs.
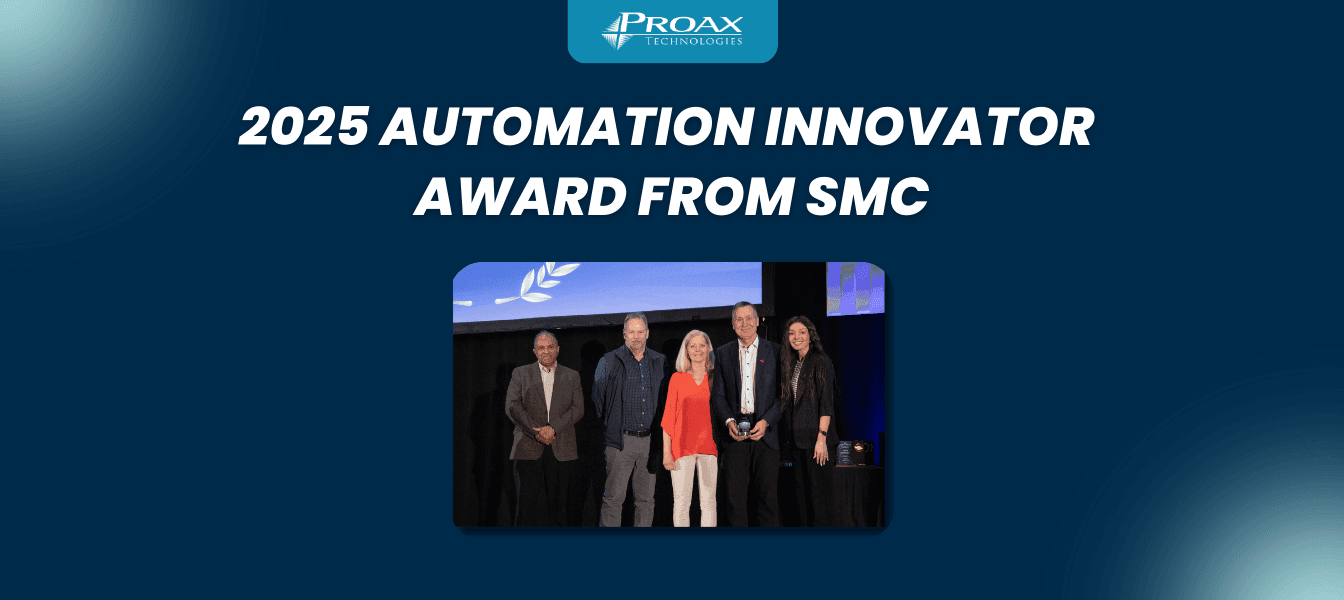
NewsProax Wins SMC 2025 Automation Innovator Award
Apr 24, 2025|
We’re thrilled to announce that Proax Technologies has received the 2025 Automation Innovator Award from SMC, a global leader in pneumatic and automation solutions.
This prestigious award recognizes Proax’s outstanding contributions in delivering innovative pneumatic systems, custom-engineered solutions, and energy-efficient automation technology to manufacturers across Canada. As an SMC Elite Distributor, this achievement reflects the strength of our collaboration and the engineering excellence behind every solution we offer.
In-House Engineering & Pneumatic Circuit Design
At Proax, we go far beyond distribution. Our in-house engineering team provides expert support for:
* Component selection and sizing
* Customized pneumatic circuit design
* Post-installation troubleshooting and consultation
Our pneumatic specialists are equipped with tools to simulate and develop application-specific circuits. From simple control systems to complex manifold layouts, we ensure every solution is optimized for efficiency, performance, and reliability.
Explore our full pneumatics product offering to discover solutions tailored for your operation.
Reduce Energy Costs with SMC's AMS System
Energy efficiency is more than a goal — it’s a competitive advantage. That’s why Proax proudly integrates SMC’s AMS Series Air Management System into our customer solutions.
This smart system enables:
* Real-time monitoring of pressure, temperature, and flow
* Programmable pressure reduction and shutdown scheduling
* Data collection via fieldbus and OPC UA protocols
By reducing air consumption and providing actionable insights, the AMS Series helps businesses make data-driven decisions that improve sustainability, lower operating costs, and extend machine life.
Download SMC AMS Series Datasheet
Local Expertise, National Reach
With locations coast to coast, Proax offers unmatched support wherever your operations are based — from British Columbia to Newfoundland. Our local teams deliver:
* Rapid response times
* On-site technical support
* Personalized service for your region
Whether you need support in Vancouver, Calgary, Toronto (Mississauga), Cambridge, Montreal, Halifax, or anywhere in between, our national footprint ensures consistent quality, fast delivery, and local expertise.
Ready to partner with one of Canada’s most trusted pneumatic automation providers?
Start your journey today: Explore SMC at Proax or contact us now.
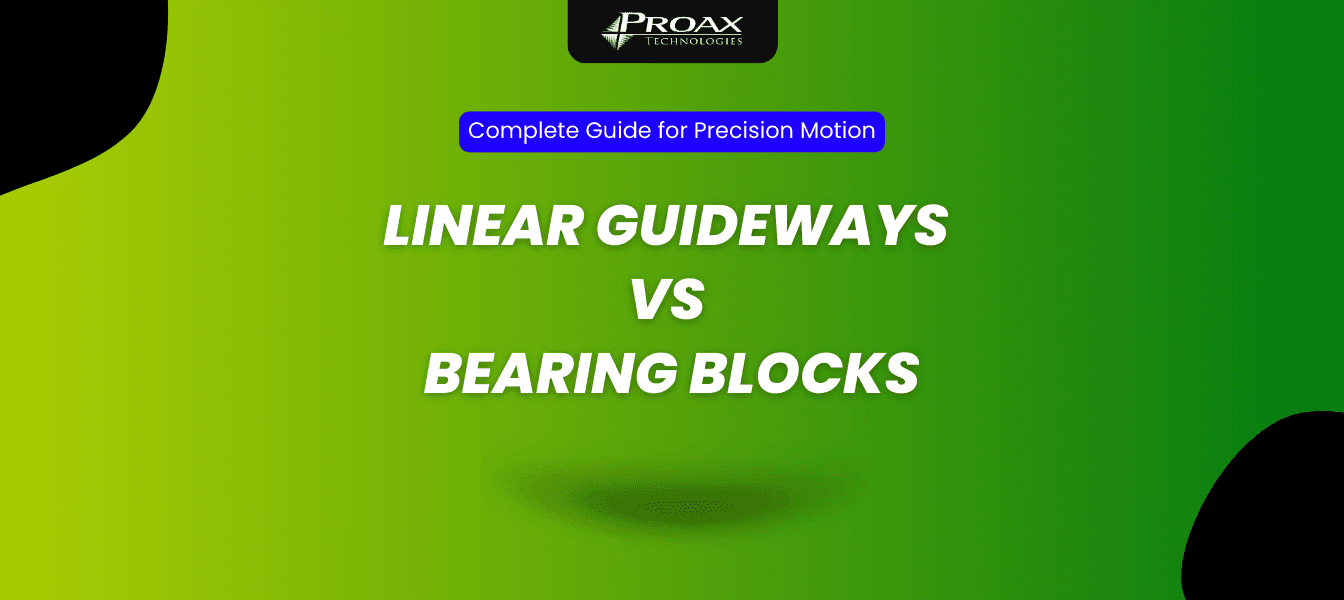
AutomationLinear Guideways vs Bearing Blocks: Complete Guide for Precision Motion
Apr 23, 2025|
Linear guideways and bearing blocks are critical components in high-performance automation, CNC machinery, robotics, and precision systems. As an authorized distributor of Hiwin, Proax Technologies offers a wide range of linear motion solutions designed to maximize efficiency, accuracy, and reliability.
What Are Linear Guideways?
Linear guideways (also known as linear bearings or motion guides) are mechanical systems that enable smooth, low-friction movement along a straight path. By using re-circulating rolling elements between a profiled rail and a bearing block, they deliver:
* High precision and repeatability
* Low friction (1/50 that of traditional sliding guides)
* Consistent smooth motion
* High load capacity in all directions
These features make them ideal for applications where accuracy and speed are critical.
How Do Linear Guideways Work?
A typical linear guideway consists of two parts:
* Rail (profiled rail): The stationary base mounted to the frame
* Bearing block: The moving carriage that houses recirculating balls or rollers
The rolling elements within the block provide linear motion with minimal resistance, making them suitable for high-speed or heavy-duty applications.
Hiwin Bearing Blocks: Types and Features
Hiwin offers both square and flange-type bearing blocks, each optimized for different load directions and mounting conditions:
* Flange Type Blocks: Lower height, ideal for heavy moment loads
* Square Type Blocks: Compact and suitable for standard applications
Key features include:
* Seals and scrapers to block contaminants
* Self-aligning designs like the HG and RG series for easy installation
* Interchangeability across rails and blocks within the same series
Explore the full bearing block selection to find the right fit.
Comparison of Hiwin Guideway Series
Series
Load Range
Key Features
HG
11.38 – 208.36 kN
Self-aligning, high speed, high rigidity, equal load in all directions
EG
5.35 – 33.35 kN
Low profile, high rigidity, compact, space-saving
CG
High Moment Load
O-type design, stainless cover strip, optimized bearing circulation
RG
11.3 – 275.3 kN
Roller type, ultra-high rigidity, 45° contact angle
WE
5.23 – 29.8 kN
Wide rail, low profile, self-aligning
MG
0.68 – 8.93 kN
Miniature, stainless steel, anti-corrosion, high stiffness
← Scroll horizontally to view more →
Selecting the Right Hiwin Linear Guideway
Before choosing your guideway and block, evaluate the following:
* Load direction & magnitude – Radial, reverse radial, and lateral
* Speed & acceleration requirements – For high-speed machines, QH or QE series with SynchMotion™ technology may be optimal
* Mounting space constraints – EG and WE series are ideal for low-profile installations
* Noise levels & smoothness – SynchMotion™-equipped models offer quieter, more stable motion
* Working environment – Consider protective seals and stainless steel if exposed to debris or corrosive agents
Applications
Hiwin linear guideways and blocks are used in:
* CNC machines
* Robotics
* Packaging and labeling equipment
* Semiconductor and medical devices
* High-speed pick-and-place systems
Final Thoughts
Whether you're building a new machine or upgrading your linear motion system, Proax's lineup of Hiwin linear guideways and bearing blocks offers proven performance across every industrial segment. With premium features, high load capacity, and unmatched precision, Hiwin remains a top choice in motion technology.
Need help choosing the right configuration? Contact our team for personalized guidance or start browsing our linear motion solutions today.
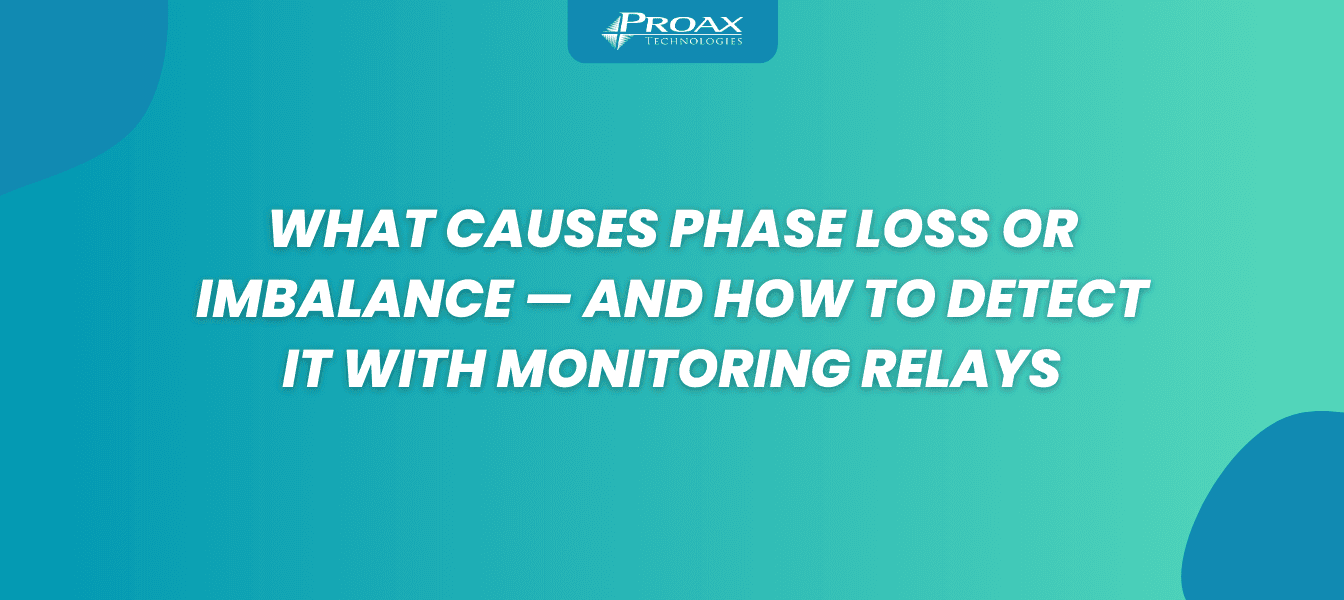
AutomationWhat Causes Phase Loss or Imbalance — and How to Detect It with Monitoring Relays
Apr 22, 2025|
Three-phase electrical systems are the backbone of industrial and commercial power distribution, prized for their efficiency and reliability. However, these systems are vulnerable to phase loss and phase imbalance, which can result in serious consequences like equipment failure, costly downtime, and safety hazards.
In this guide, we’ll break down:
* What causes phase issues
* Their consequences
* How to detect them with monitoring relays
* Practical prevention strategies
What is Phase Loss and Phase Imbalance?
* Phase Loss (Single Phasing): One of the three electrical phases is lost or significantly reduced, forcing the remaining two to compensate. This causes motors to draw unbalanced currents and quickly overheat.
* Phase Imbalance: Voltage or current between the three phases becomes uneven, even if all phases are technically still operating.
Common Causes of Phase Issues
Cause
Description
Blown Fuses or Tripped Breakers
One disconnected fuse can break the entire phase chain.
Damaged or Aged Cables
Mechanical damage or insulation failure can disconnect a phase.
Loose or Corroded Connections
Terminal posts and connectors degrade over time, leading to intermittent phase loss.
Unbalanced Loads
Connecting large single-phase loads unevenly causes imbalance.
Aging Infrastructure
Old transformers, worn relays, or outdated panels increase risk.
Improper Protection Settings
Incorrectly set overloads or VFDs may not react during faults.
Environmental Conditions
Weather events, wildlife, or pole damage can suddenly knock out a phase.
Integration of Renewables
Intermittent solar or wind sources can destabilize phases if unmanaged.
Motor Winding Failure
Insulation degradation in motor windings contributes to phase loss internally.
← Scroll horizontally to view more →
Consequences of Phase Loss and Imbalance
* Equipment Overheating: Motors draw excessive current on remaining phases.
* Vibration and Performance Loss: Motors may stall or rotate in reverse.
* Reduced Lifespan: Even a 5% imbalance can cut motor capacity by 25%.
* Harmonics & Flickering: Poor power quality affects sensors, controllers, and lighting.
* Safety Risks: Overheated components pose fire and electrical hazards.
How to Detect Phase Issues Using Monitoring Relays
Monitoring relays are dedicated devices that continuously check the integrity of all three phases. When something’s off—they act fast.
For example, 3-phase monitoring relays are used to detect phase loss, asymmetry, and incorrect phase sequence. You can explore models like the Omron K8AK-PW or K8DS-PM, or opt for Phoenix Contact options such as the EMD-SL-PH-690 and EMD-SL-3V-400, both of which offer robust protection for voltage phase monitoring.
If you're dealing with individual line issues, 1-phase monitoring relays like the Omron K8AK-AS and K8AK-VS are reliable options.
For thermal protection or heating applications, devices such as the K8AK-TH offer precise temperature monitoring. You can view our full range of monitoring products here.
Product Comparison Table
Model
Type
Key Features
Voltage Range
Brand
K8AK-PW
3-Phase
Over/undervoltage
3-wire/4-wire
Omron
K8AK-AS
1-Phase
Over/undercurrent
0.1–30A
Omron
EMD-SL-PH-690
3-Phase
Sequence, failure, asymmetry
208–690V AC
Phoenix
K8AK-VS
1-Phase
Over/undervoltage
200–240V AC
Omron
EMD-SL-3V-400
3-Phase
Window voltage monitoring
280–520V AC
Phoenix
← Scroll horizontally to view more →
Prevention Tips and Best Practices
Action
Benefit
Routine Maintenance
Catch wear and corrosion before failure.
Even Load Distribution
Prevents phase imbalance and inefficiency.
Upgrade Equipment
Faster response to faults.
Continuous Monitoring
Real-time alerts prevent unplanned downtime.
← Scroll horizontally to view more →
Frequently Asked Questions
What causes phase loss in a 3-phase system?
Blown fuses, loose wiring, or damaged cables are common causes.
How do I detect a phase imbalance?
Use a 3-phase monitoring relay like K8AK-PW or EMD-SL-PH-690 to detect imbalances in real time.
What are the risks of ignoring phase imbalance?
Reduced motor life, overheating, harmonics, and fire risks.
Can these relays be installed in older panels?
Yes, most models are DIN rail mountable and retrofit-ready.
Final Thoughts
Phase loss and imbalance are preventable yet critical threats in industrial systems. With monitoring relays and proactive strategies, you can avoid catastrophic damage, reduce downtime, and extend asset life.
Explore our wide selection of 3-phase and 1-phase monitoring relays — backed by expert support and fast Canadian shipping.
Not sure what you need? Talk to our experts today.
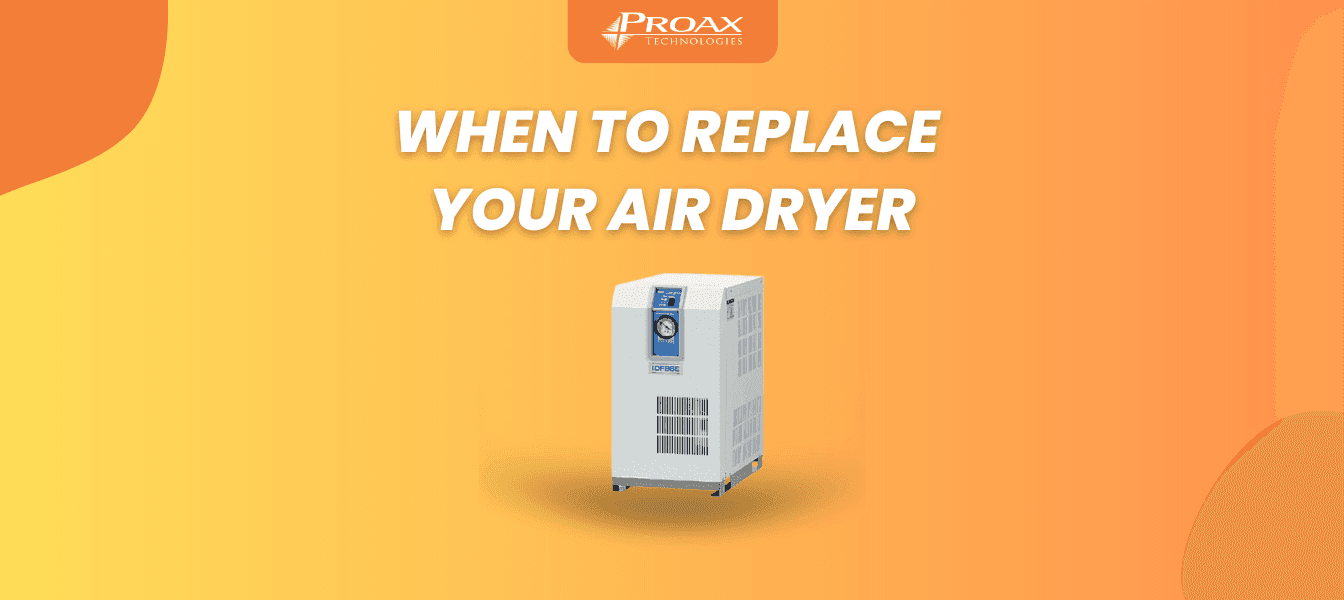
AutomationWhen to Replace Your Pneumatic Air Dryer: Essential Guide for Canadian Industries
Apr 21, 2025|
In industrial settings across Canada, pneumatic air dryers are the unsung heroes of compressed air systems. These vital components remove moisture and contaminants, protecting your valuable equipment and ensuring quality production. But even the most reliable air dryers have a finite lifespan—and knowing when to replace them can save your operation from costly downtime and equipment damage.
At Proax, we've helped countless Canadian businesses optimize their pneumatic systems. In this comprehensive guide, we'll walk you through the telltale signs that it's time for a replacement and provide expert maintenance tips to extend your air dryer's service life.
Why Air Dryer Replacement Timing Matters
The consequences of running with a failing air dryer extend far beyond minor inconveniences:
* Equipment Protection: Moisture in compressed air lines leads to rust, corrosion, and premature tool failure—often resulting in thousands of dollars in damage
* Production Quality: In painting, food processing, or pharmaceutical applications, even minimal moisture contamination can ruin entire production batches
* Energy Efficiency: A struggling air dryer forces your compressor to work harder, potentially increasing energy consumption by 10-25%
* Operational Reliability: Sudden air dryer failure can bring production to a complete standstill, creating costly delays and missed deadlines
6 Clear Signs You Need to Replace Your Air Dryer
1. Moisture Detection in Your System
The primary purpose of an air dryer is moisture removal. If you're noticing:
* Water droplets in air lines or at point-of-use
* Rust forming inside pneumatic tools
* Condensation in air storage tanks
* Water blowing from pneumatic outlets
These are unmistakable indicators that your air dryer is no longer functioning properly and requires replacement.
2. Increasing Maintenance Frequency
Are you finding yourself calling technicians more often for your air dryer? When repair costs and frequency increase, it's often more economical to invest in a new unit. Compare your maintenance logs—if service calls have doubled in the past year, replacement is likely the smarter financial decision.
3. Rising Energy Consumption
An inefficient air dryer creates back pressure that forces your compressor to work harder. Review your energy bills—a gradual increase in electricity costs without corresponding production increases often points to air treatment system issues. New refrigerated air dryers can provide significant energy savings compared to older models.
4. Physical Deterioration
Visual inspection can reveal a lot about your air dryer's condition:
* Visible external corrosion or rust
* Cracked components or housings
* Leaking connections or fittings
* Damaged gauges or controls
These physical signs indicate environmental stress and aging that compromise performance.
5. Pressure Drop Issues
Monitor the pressure differential across your air dryer. A healthy system maintains consistent pressure, while a failing unit will show:
* Increased pressure drop across the dryer (exceeding manufacturer specifications)
* Inability to maintain system pressure during peak demand
* Longer recovery times after air usage
6. Excess Water from Purge Valves
Modern air dryers should produce minimal condensate during normal operation. If your purge valve is constantly discharging water, your dryer is struggling to remove moisture effectively.
Recommended Replacement Schedules
While every operation is different, these industry-standard replacement intervals provide solid guidelines:
Component
Replacement Timeline
Warning Signs
Dryer Filters
Every 2,000 operating hours or annually
Pressure differential increase, visible contamination
Desiccant (for desiccant dryers)
Every 3-5 years
Color change, reduced efficiency
Pre/Post Filter Elements
Every 12 months
Excessive pressure drop, visible contamination
Control Air Filter Elements
Every 12 months
Erratic controller operation
Refrigerated Dryer
8-10 years (depending on usage)
Increasing energy usage, moisture breakthrough
← Scroll horizontally to view more →
Note: For specialized applications like pharmaceutical or food production, more frequent replacement may be necessary to maintain air quality standards.
Maximizing Your Air Dryer Lifespan: Maintenance Best Practices
Proper maintenance can significantly extend your air dryer's service life:
Daily Checks
* Monitor pressure differentials across filters
* Check moisture indicators and dew point (when applicable)
* Listen for unusual sounds (particularly in refrigerated air dryers)
Monthly Maintenance
* Inspect and clean condenser coils on refrigerated models
* Check all drain functions
* Examine for air or refrigerant leaks
* Clean or replace standard filters as needed
Annual Service
* Complete system evaluation
* Replace all filter elements
* Check electrical connections and controls
* Calibrate sensors and gauges
Choosing Your Replacement: Technology Advancements
When replacing your air dryer, consider these recent advancements that could benefit your operation:
Energy-Efficient Models
Modern IDFB refrigerated air dryers offer significant energy savings compared to older technologies. These units adjust cooling capacity based on actual demand, reducing power consumption during partial loads—often resulting in 25-50% energy savings.
Smart Monitoring Capabilities
Today's premium air dryers feature digital controls and remote monitoring capabilities. These systems:
* Provide real-time performance data
* Alert maintenance teams to potential issues before failure
* Track energy usage and efficiency metrics
* Allow for preventive rather than reactive maintenance
Environmental Considerations
Newer refrigerated dryers use environmentally friendly refrigerants with lower global warming potential, helping your operation meet sustainability goals while complying with evolving regulations.
Conclusion: Partner with Experts for Optimal Results
Replacing your pneumatic air dryer at the right time isn't just about avoiding problems—it's about optimizing your entire compressed air system for reliability, efficiency, and performance.
At Proax, we're proud to be authorized SMC distributor across Canada, offering expert guidance on air treatment solutions tailored to your specific industry needs. Our team can help you determine the ideal replacement timing, select the right technology for your application, and ensure proper installation for maximum performance.
Don't wait for a system failure to consider replacement. Contact our compressed air specialists today for a comprehensive evaluation of your current air dryer performance and expert recommendations on upgrading your system.
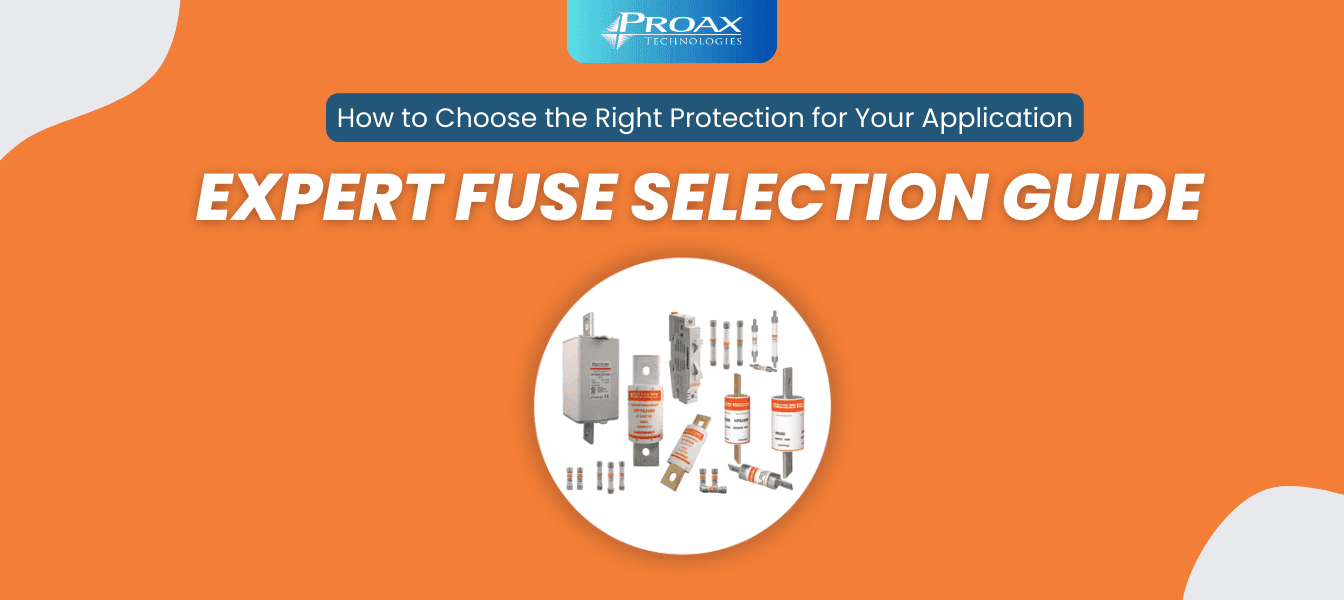
SafetyExpert Fuse Selection Guide: How to Choose the Right Protection for Your Application
Apr 17, 2025|
Selecting the right fuse for your electrical system isn't just about matching numbers—it's a critical design decision that directly impacts safety, reliability, and performance. At Proax, we understand that proper fuse selection can mean the difference between smooth operations and costly downtime or even dangerous failures.
Why Proper Fuse Selection Is Critical
A fuse serves as the intentional "weakest link" in your electrical circuit, designed to sacrifice itself when dangerous current levels threaten your equipment and personnel. But choosing the wrong fuse can lead to:
* Nuisance trips that interrupt operations unnecessarily
* Equipment damage from inadequate protection
* Safety hazards from improper interruption capabilities
* Compliance issues with industry standards and regulations
Let's explore the essential factors to consider when selecting the right fuse for your specific application needs.
Key Selection Criteria for Fuses
1. Current Rating: Finding the Sweet Spot
The current rating of your fuse should be carefully calculated to match your application's normal operating conditions while providing protection against overloads.
Best Practice: Select a fuse with a current rating approximately 125% of your circuit's maximum normal operating current. For example, if your circuit typically draws 8A, a 10A fuse provides an appropriate safety margin.
Application Consideration: Different loads have different current profiles:
* Motor circuits experience high inrush currents during startup
* Transformer circuits can experience magnetizing inrush when energized
* Electronic circuits may need tighter protection margins
2. Voltage Rating: Never Compromise
A fuse's voltage rating must always meet or exceed the maximum voltage in your circuit—no exceptions.
Safety Rule: Choose a fuse with a voltage rating at least 20% higher than your system's maximum operating voltage to account for transients and fluctuations.
Important Distinction: AC and DC applications require different considerations:
-AC fuses benefit from natural current zero-crossing for arc extinction
-DC fuses must be specifically rated for DC use, as interrupting DC is more challenging
3. Breaking Capacity: Prepared for the Worst
The fuse's interrupting capacity (also called breaking capacity) must exceed the maximum fault current available in your system.
Critical Safety Factor: Underestimating available fault current is dangerous—a fuse that cannot safely interrupt a fault may rupture violently or allow continued current flow.
Calculation Tip: Work with your electrical engineer to determine the maximum available fault current at the installation point, then select a fuse with an interrupting rating that exceeds this value with margin.
4. Time-Current Characteristics: Speed Matters
Different applications require different fuse response speeds:
Response Type
Characteristics
Typical Applications
Fast-Acting
Quickly responds to overloads
Electronic protection, semiconductor safeguarding
Time-Delay
Tolerates temporary overloads
Motors, transformers, and loads with inrush currents
Very Fast-Acting
Extremely rapid response
Sensitive semiconductor protection
Application Matching: Select time-current characteristics based on normal operating conditions. For example, motors that draw 6-8 times their rated current during startup require time-delay fuses to prevent nuisance tripping.
5. Environmental Factors: The Often Overlooked Consideration
Ambient conditions significantly impact fuse performance:
Temperature Effects: Fuses are typically rated at 25°C (77°F). Higher ambient temperatures require derating:
* At 60°C (140°F), you may need to increase fuse size by 15-25%
* At lower temperatures, fuse clearing time may increase
Installation Environment: Consider exposure to:
* Vibration and mechanical stress
* Humidity and corrosive atmospheres
* Altitude (affects air's dielectric strength)
Mersen Fuse Series: Finding Your Perfect Match
As an authorized Mersen distributor, Proax offers access to Mersen's comprehensive range of high-quality fuses. Here's how to match Mersen series to your specific application needs:
Class J Fuses: Versatile Protection for Industrial Applications
A4J Series (Fast-Acting)
* Best For: General power distribution, feeders, and loads requiring quick response
* Key Features: Excellent current-limiting protection, 600VAC/300VDC rating
* Interrupting Rating: Up to 200kA
* Application: Ideal for general circuits without significant inrush current
AJT Series (Time-Delay)
* Best For: Motor circuits, transformers, and branch circuits
* Key Features: Superior current-limiting with time-delay, SmartSpot indicator
* Voltage Rating: 600VAC/400VDC
* Application: Perfect for applications with high inrush currents that need time-delay protection
Class CC Fuses: Compact Protection for Small Circuits
ATDR Series (Time-Delay)
* Best For: Small motors, branch circuits, and control systems
* Key Features: Best time-delay characteristics in its class, excellent cycling capacity
* Electrical Ratings: 600VAC/300VDC, 200kA interrupting capacity
* Application: Ideal for small motor protection and sensitive branch circuits
Miniature Fuses: Protection for Electronic Applications
GDL Series (Time-Delay)
* Best For: Electronic circuits requiring time-delay
* Form Factor: Glass, miniature (1/4" × 1-1/4")
* Voltage Rating: Up to 250VAC
* Application: Electronic equipment with temporary overloads
GGC Series (Fast-Acting)
* Best For: Sensitive electronic protection
* Form Factor: Glass, miniature (1/4" × 1-1/4")
* Current Range: 1/10A–30A
* Application: Electronic circuits requiring quick response
GSA Series (Time-Delay)
* Best For: High-current electronics
* Form Factor: Ceramic, miniature (1/4" × 1-1/4")
* Application: Equipment like microwave ovens that need time-delay protection
GSB Series (Fast-Acting)
* Best For: Electronic circuit protection requiring speed
* Application: Fast protection for sensitive electronic equipment
Selection Methodology: A Step-by-Step Approach
Follow these steps to select the optimal fuse for your application:
1. Define Your Circuit Parameters:
* Normal operating current
* Maximum system voltage
* Available fault current
* Load characteristics (resistive, inductive, motor, etc.)
2. Identify Special Considerations:
* Inrush current requirements
* Ambient temperature conditions
* Space constraints
* Required agency approvals
3. Select Fuse Class and Series:
* Match application needs to appropriate fuse class
* Choose time-current characteristics (fast-acting vs. time-delay)
4. Verify Ratings Meet or Exceed Requirements:
* Current rating (with appropriate margin)
* Voltage rating (equal to or greater than system voltage)
* Interrupting capacity (greater than available fault current)
5. Confirm Physical Installation Requirements:
* Mounting method compatibility
* Space availability
* Accessibility for maintenance
Fuse Selection Checklist
Selection Criteria
What to Verify
Common Pitfalls to Avoid
Current Rating
Exceeds normal load by appropriate margin
Oversizing reduces protection; undersizing causes nuisance trips
Voltage Rating
≥ Maximum circuit voltage (with safety margin)
Using AC-rated fuses in DC applications
Interrupting Capacity
> Maximum available fault current
Underestimating available fault current
Application Type
Matches load characteristics (motor, electronic, etc.)
Using fast-acting fuses with inrush loads
Ambient Temperature
Consider derating for temperatures above 25°C
Failing to adjust for high-temperature environments
Agency Approvals
Meets UL, CSA, IEC requirements as needed
Missing required certifications for your application
Future-Proofing Your Protection Strategy
When designing electrical systems, consider these forward-looking approaches:
* Anticipate Growth: Select fuses with some headroom if system expansion is likely
* Standardize Where Possible: Reduce inventory and maintenance complexity
* Consider Coordination: Ensure proper selectivity between upstream and downstream protection devices
* Document Your Selections: Maintain records of fuse selections and the reasoning behind them
Expert Support When You Need It
At Proax, we understand that fuse selection can be complex. Our in-house technical specialists can help you navigate the selection process and ensure optimal protection for your specific application.
Explore our complete range of industrial fuses and benefit from our status as an authorized distributor for Mersen, a global leader in electrical power and advanced materials.
Whether you're designing a new system or upgrading existing protection, our team is ready to help you select the right fuse for your application—because when it comes to electrical protection, there's no room for compromise.
Contact us today to discuss your specific protection needs and discover why Proax is the trusted partner for electrical protection solutions.