Picture this: your bottling line is running at full speed, but you're constantly worried about defective products slipping through inspection. Misaligned caps damage equipment downstream, contamination issues create costly recalls, and your brand reputation hangs in the balance with every bottle that leaves the facility.
This scenario recently played out for a major North American bottled water manufacturer, and the solution they implemented showcases how advanced machine vision technology can transform quality control while maintaining production speeds exceeding 1,000 bottles per minute.
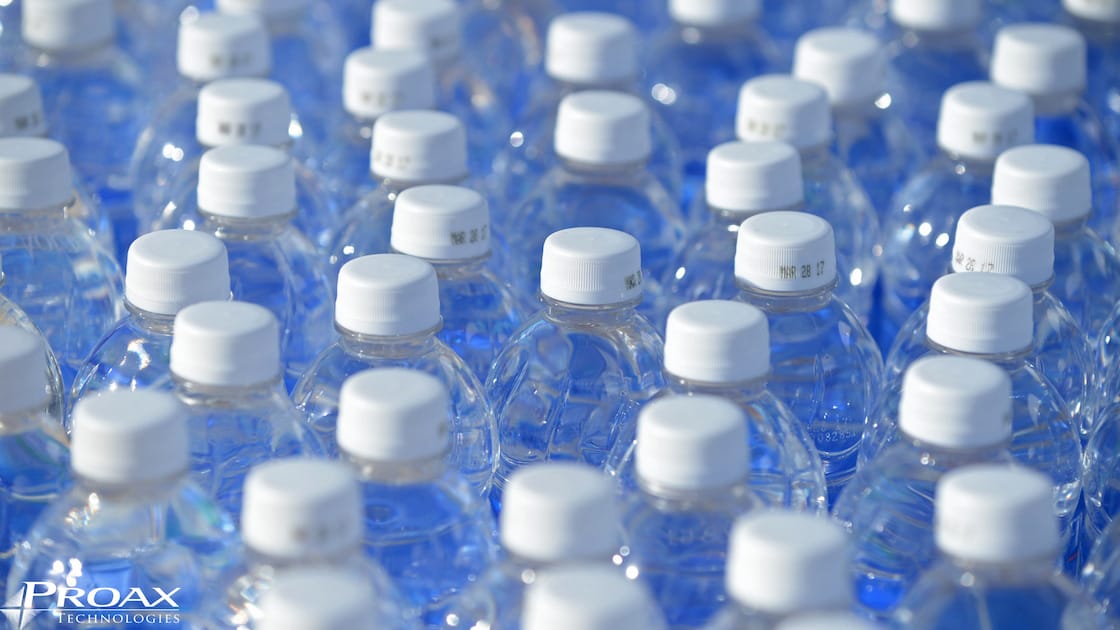
The Industry Challenge: Speed vs. Quality in Beverage Production
The beverage industry faces unique quality control challenges that traditional inspection methods struggle to address effectively. This particular manufacturer was experiencing significant issues with their existing bottle inspection system:
- Inadequate cap detection: Bottle caps with small trapezoidal surfaces couldn't be properly evaluated
- Critical blind spots: Two-camera systems missed tilted caps in certain orientations
- Equipment damage: Misaligned caps were damaging downstream machinery
- Quality escapes: Defective products reaching consumers and threatening brand integrity
These challenges are common across the beverage industry, where high-speed production lines demand both speed and precision.
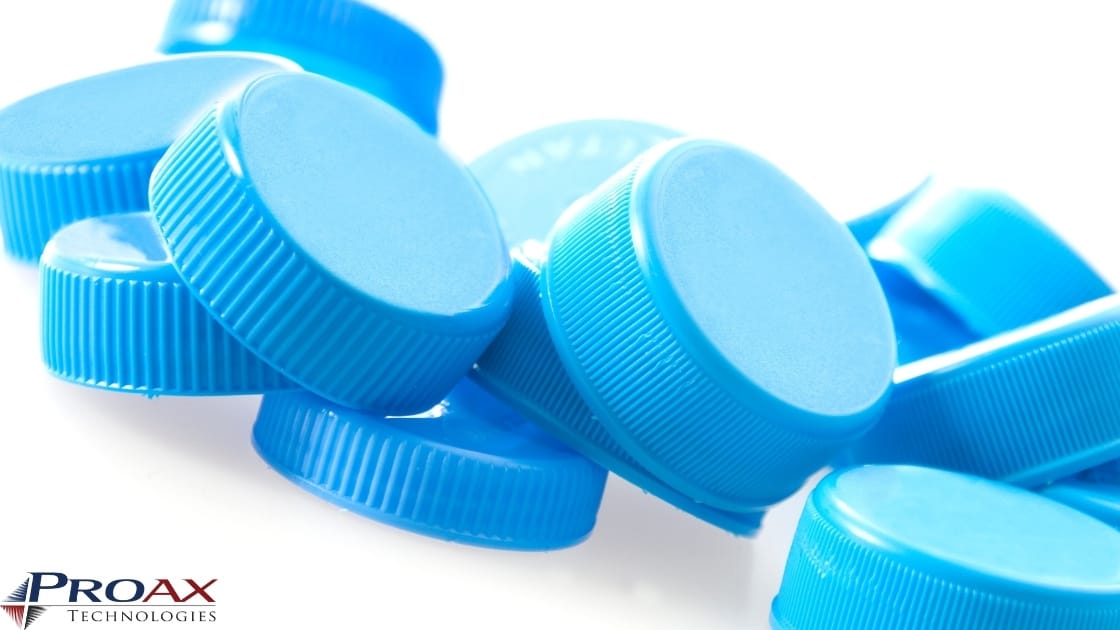
Understanding Beverage Industry Quality Requirements
Cap placement and seal integrity are fundamental to beverage quality and safety. Common issues that can compromise production include:
- Plastic burrs interfering with proper cap placement
- Misaligned or upside-down caps during feeding
- Cap feeder jams and equipment malfunctions
- Malformed bottle necks affecting seal quality
- Improper threading causing loose or over-tightened caps
- Production changeovers introducing tolerance variations
When these defects go undetected, the consequences extend throughout the supply chain, affecting equipment reliability, product safety, and brand reputation.
The Technology Solution: High-Speed Vision Inspection
As an authorized Omron distributor, Proax recognizes the power of advanced vision sensors and systems in addressing these critical beverage industry challenges. The manufacturer's success story showcases what's possible with the right technology approach.
How FH Vision Systems Achieve 1,000+ Bottles Per Minute Inspection
The Omron FH vision system delivers exceptional performance for high-speed beverage applications through several key capabilities:
High-Speed Processing Power
- High-speed CMOS cameras capture clear images at production speeds
- Simultaneous processing of up to four images ensures comprehensive inspection
- Real-time decision making keeps pace with fast production lines
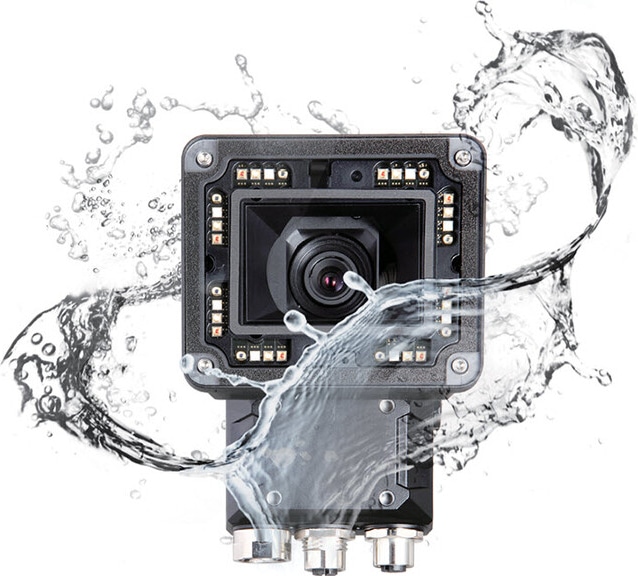
Complete Quality Coverage
- Liquid-level verification ensures proper fill volumes
- Cap placement and integrity monitoring prevents seal failures
- Tamper-band inspection confirms security features
- Label positioning and quality verification
Advanced Code Reading Capabilities The system excels at critical traceability requirements:
- Date code, lot code, and factory code verification
- Comparison against system time and location data
- Reliable reading of both ink-printed and laser-marked codes
- Proven performance on curved, compressed, elongated, or damaged codes
Strategic Camera Positioning for Complete Coverage
The successful implementation utilized strategic camera placement to eliminate blind spots:
- Two cameras positioned 90 degrees apart
- 45-degree angle to bottle flow for optimal visibility
- Four inspection points at 90-degree intervals around each cap
- Complete 360-degree monitoring of critical quality parameters
Measurable Results in Beverage Production
The implementation delivered significant operational improvements:
Quality Achievements
- 100% inspection coverage eliminating quality escapes
- Zero blind spots ensuring comprehensive defect detection
- Automated verification removing manual inspection requirements
- Consistent quality standards across all production shifts
Operational Benefits
- Reduced product waste through early defect detection
- Equipment protection preventing downstream damage
- Eliminated contamination from seal integrity issues
- Decreased customer complaints and returns
Business Impact
The success was so significant that the manufacturer expanded the solution to seven additional facilities nationwide, demonstrating the scalability and reliability of the technology.
Why Choose the Right Technology Partner
At Proax, we understand the unique challenges facing beverage manufacturers. Our expertise in vision sensors and systems combined with our status as an authorized Omron partner ensures access to cutting-edge technology and comprehensive support for both end users and system integrators.
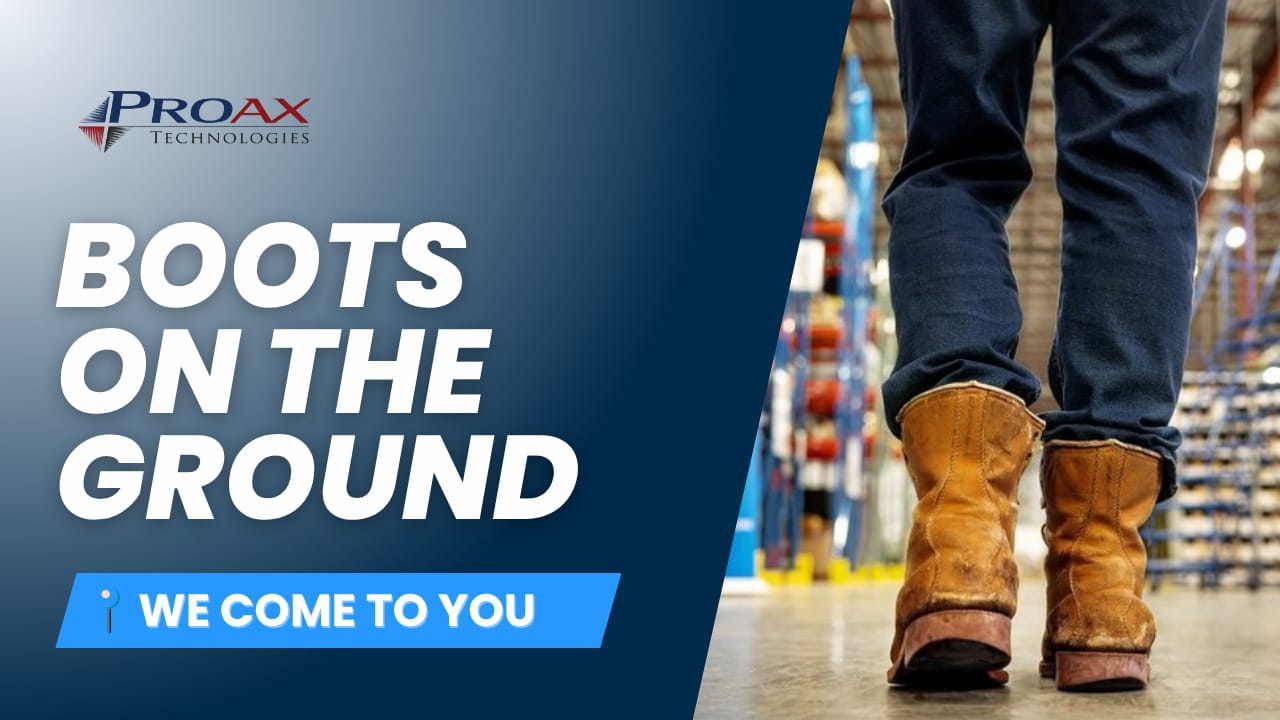
Our "Boots On the Ground" Approach
We're currently running our "Boots On the Ground" campaign, where we come to your facility for free to solve your production bottlenecks. This proven process identifies and solves challenges in a single visit:
1. Pre-Visit Preparation
- We gather information about your facility and specific needs to prepare for an effective visit
2. On-Site Assessment
- Our sales and technical teams along with Omron specialists conduct a thorough assessment
3. Customized Solutions
- We develop tailored solutions with our product offerings and in-house technical capabilities based on our assessment and your specific requirements
Supporting Your Success
- Application analysis: Understanding specific production requirements
- Technical consultation: Providing expert guidance on optimal solutions
- Product availability: Ensuring reliable supply and support
- Performance optimization: Helping maximize throughput and quality results
Technology Advantages for Beverage Applications
The Omron FH Series vision system offers several advantages specifically beneficial for beverage production:
Scalability and Flexibility
- Support for up to 16 cameras for complex multi-station inspection
- Compatibility with various GigE Vision cameras
- Adaptable to different bottle sizes and production configurations
Real-Time Intelligence
- Manufacturing process monitoring and statistical process control
- Immediate feedback for process adjustments
- Data logging for quality compliance and traceability
User-Friendly Operation
- Menu-driven software simplifies setup and operation
- PC-based integration for familiar interface
- Comprehensive diagnostic capabilities
Applications Beyond Basic Inspection
Modern vision systems can address multiple beverage industry requirements simultaneously:
- Product identification: Verify correct products on specific lines
- Label inspection: Ensure proper placement, print quality, and compliance
- Date and lot coding: Critical for traceability and recall management
- Fill level consistency: Maintain consumer satisfaction and regulatory compliance
- Packaging integrity: Detect damage or contamination before shipping
Ready to explore vision system solutions for your applications? Contact us today to discuss your requirements and discover how proven inspection technology can deliver the reliability and performance your projects demand.