When it comes to air treatment systems, air dryers hold a pivotal role, especially in industrial applications. But what exactly is an air dryer, and how does it work? What are the different types of air dryers available, and which one is the right fit for you? We'll delve into all these questions in this blog post, also outlining the distinction between air compressors and air dryers. So, let's get started!
What is an Air Dryer?
An air dryer is an essential piece of equipment often used in conjunction with compressed air systems. It serves to remove water vapor from the compressed air. By doing so, it helps protect the system from potential damage caused by the condensation of water vapor in the system, a critical task, especially in humid climates and demanding industrial applications.
What Does an Air Dryer Do?
Now that we know what an air dryer is, let's understand its function more closely. An air dryer works to dehumidify or "dry" the air by effectively removing water vapor. The process is integral in industries like manufacturing, automotive, and power plants, where water in the air can cause significant harm, leading to rust, corrosion, and even malfunction of equipment.
Through drying the air, air dryers maintain the integrity of your systems, enhancing performance, extending life, and reducing maintenance costs.
Types of Air Dryers
Air dryers come in different types, each designed to cater to specific applications and requirements. Here are the most common types of air dryers:
Refrigerated Air Dryers
Refrigerated Air Dryers are the most widely used type of air dryer. They function much like your refrigerator at home, by cooling the incoming air to a point where the moisture condenses. This water is then drained out, leaving the air dry. Refrigerated air dryers are typically used in general industrial applications where the requirement for dryness isn't overly stringent.
A refrigerated air dryer is a popular choice for many industries due to its energy efficiency and cost-effectiveness. The main function of a refrigerated air dryer is to decrease the temperature of the compressed air, which leads to condensation and, ultimately, water removal. Here's a step-by-step look at the process:
Compressed Air Entry: The warm, moist compressed air enters the air dryer.
Air Cooling: The incoming air is first precooled in an air-to-air heat exchanger. This step is critical for energy efficiency. The outgoing cold, dry air cools the incoming warm, moist air.
Refrigeration Cycle: The air then goes into an air-to-refrigerant heat exchanger. Here, it's further cooled down to a temperature just above freezing, leading to the condensation of water vapor present in the air.
Water Separation and Drainage: The condensed water droplets are then separated out from the air stream, usually using a centrifugal separator or another type of moisture separator and drained off.
Air Reheating: Finally, the cold, dry air is reheated in the air-to-air heat exchanger by the incoming air. This step prevents downstream pipe sweating and also aids in the overall energy efficiency of the system.
The result is dry compressed air, devoid of moisture, which is now suitable for use in various tools and machinery without the risk of water-induced damage. The dew point achieved by a refrigerated air dryer typically ranges from 35 to 50 degrees Fahrenheit, making it suitable for most general industrial applications.
Membrane Air Dryers
Membrane Air Dryers work on the principle of selective permeation. In this, compressed air passes through a membrane, with water vapor and other impurities permeating the membrane wall and the dry air passing through.
Membrane air dryers offer a unique solution to the challenge of drying compressed air. Instead of using temperature changes or chemicals to remove moisture, these systems utilize special membrane materials to separate water vapor from the air. Here's a more detailed look at the process:
Compressed Air Entry: The compressed air first enters the air dryer, bringing along its contained moisture.
Membrane Separation: The air is then passed through a bundle of specially engineered membrane fibers. These fibers have selective permeability, which means they allow certain components of the air, like water vapor and other small particles, to pass through more readily than others.
Permeation Process: As the compressed air travels along the length of the membrane fibers, water vapor permeates the walls of the fibers and is swept away by a stream of purge air, leaving dry air to continue through the system. Some systems use a portion of the dried compressed air as the purge air, while others may use a separate source of air or another gas.
Removing the water collected. Membrane dryers require a percentage of clean dry air to remove the collected water. This amount of purge air can vary depending on the dewpoint required, but generally it is between 10 to 40% of your compressed air being vented top atmosphere in removal of the water collected.
Dry Air Output: The result is clean, dry compressed air at the outlet, ready for use in your equipment or processes.
Membrane air dryers are particularly useful in applications where space is limited or where no power source is available, as they are typically compact and require no electricity. Moreover, these systems are quiet and have few moving parts, making them reliable and low maintenance. They can achieve a wide range of dew points, from around +40 degrees Fahrenheit to as low as -40 degrees Fahrenheit, making them versatile for a range of applications.
Which Compressed Air Dryer is Right for Me?
Compressed air dryers are indispensable components of a compressed air system. Although moisture in your compressor installation is unavoidable, the problems this moisture can cause downstream can be significant. Leaving this moisture in your compressor system is unacceptable, as it can contaminate final products and damage pneumatic equipment and other components. Here is where an air dryer comes into play. Dryers are one of the pieces of equipment (along with aftercoolers) that assist in drying the moist air, thereby safeguarding your installation from the adverse effects of moisture. But which sort of compressed air dryer best suits your needs?
How Do I Select an Air Compressor Dryer?
Essentially, the appropriate dryer size should dry air at whatever rate your compressor produces air to satisfy your process's needs. As with everything else on compressed air, calculation tools are available to determine the optimal dryer, and it is not advisable to rely on guesswork or simply replace what was there. Ultimately, there are six main factors to consider when selecting the proper dryer:
•Maximum air velocity in standard cubic feet per minute (scfm)
•Desired pressure dew point
•Inlet compressed air pressure
•Inlet air temperature
Temperature of the ambient air (and water, if the condenser is water-cooled).Typically, desiccant dryers can provide a dew point as low as -40°C / -40°F. Demanding applications in industries such as piping exposed to freezing, pharmaceuticals, food processing, and applications requiring extremely high-quality air can benefit from the air with a consistent, predictable dew point. Refrigerant dryers typically attain a dew point of approximately 3°C / 37°F.However, desiccant dryers have a high operating cost with energy consumption and or media replacement. A refrigerated air dryer would be an excellent choice for applications that demand dry air but do not require a critical dew point.
Should You Purchase an Air Compressor with an Integrated Dryer?
These are a popular choice generally speaking! When space is limited and dried air is required, using a compressor with an integrated dryer makes sense, but if the compressor or dryer requires repair, it often has a higher cost than if purchased separately. The dryer is designed to operate with the corresponding compressor. The entire system is in a cabinet that minimizes the required footprint. How crucial is dryer selection to overall system effectiveness? It can be particularly significant. A compressed air dryer not optimized for efficiency can easily add 25% to your overall energy bill. In contrast, a compact air dryer optimized for efficiency should contribute no more than 2%. The drying technology and dryer size you choose should align with your compressed air discharge rate and air quality specifications.
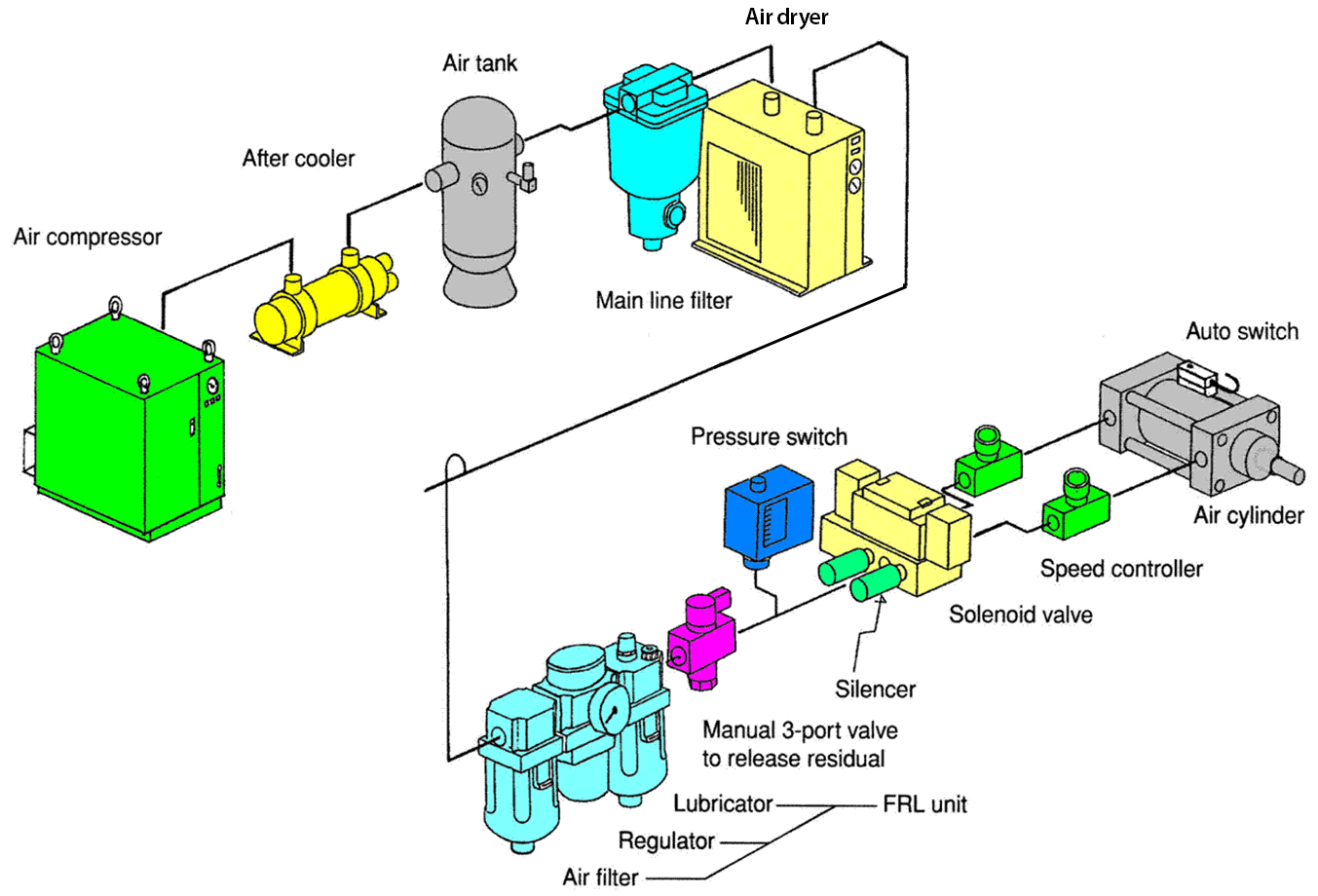
Difference between Air Compressor and Air Dryer
Air Compressor |
Air Dryer |
|
Function |
Draws in air and delivers at a
higher pressure. |
Removes moisture from
compressed air. |
Use |
Used across many industries for its speed, cleanliness, and low heat
generation. |
Paired with compressed air systems to prevent moisture-related issues. |
Types |
Reciprocating, rotary screw,
centrifugal, etc. |
Refrigerated,
dessiccant, membrane, déliquescent, etc. |
Operations |
Increases air pressure by decreasing volume. |
Reduces moisture content by chilling, absorbing, or permeating. |
Components |
Driving motor, compression
chamber, storage tank. |
Inlet, moisture removal
mechanism, outlet. |
SMC Air Dryers are devices designed to remove moisture from highly efficient compressed air. In a compact air system, moisture can be detrimental, causing corrosion, scale, and contamination. By utilizing an SMC Air Dryer, industries can prevent this damage and prolong the useful life of their pneumatic instruments and equipment.
Contact us today to discover how our team can help you select the right Air Dryers for your needs, maximize efficiency, and push the boundaries of what's possible.