Pneumatic tubing is the circulatory system of any compressed‑air network—from factory automation to hospital capsule pipelines. In this guide you’ll learn:
✔️ How pneumatic tubing systems work
✔️ Key components (carriers, stations, diverters, blowers)
✔️ Material & type breakdown (polyurethane, fluororesin, polyethylene, spark‑resistant, and more)
✔️ Sizing & selection (imperial & metric tube chart)
✔️ 2025 installation & maintenance best practices
✔️ FAQs & troubleshooting tips
Whether you’re specifying for a new installation or optimizing an existing network, this comprehensive guide will help you choose, size, install, and care for your pneumatic tubing system.
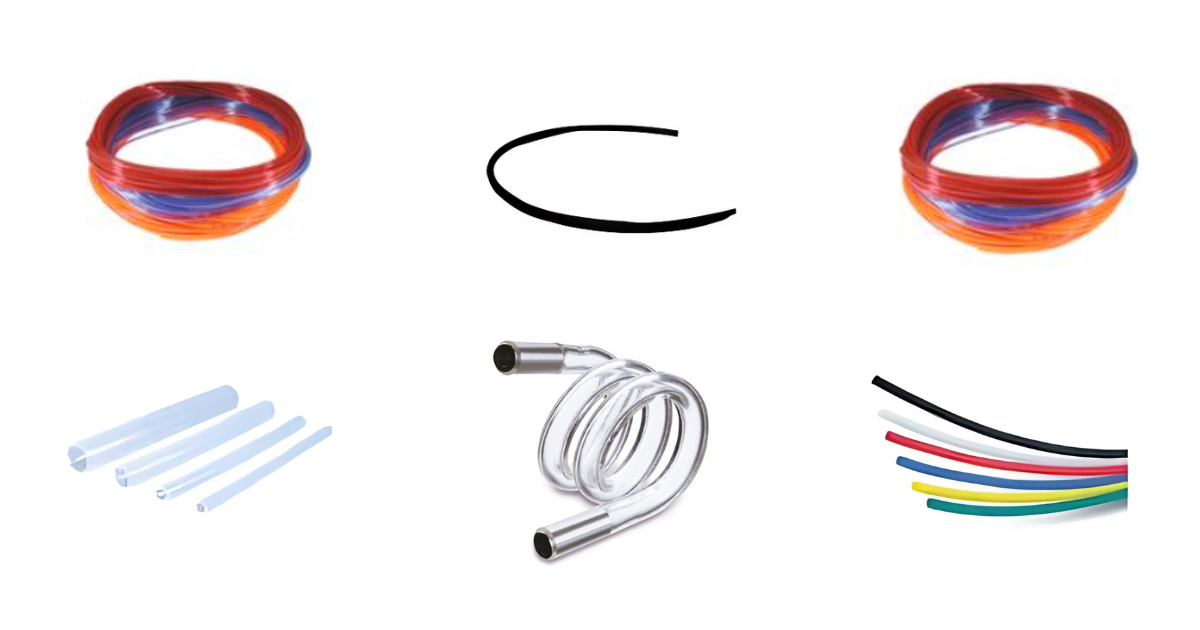
What is a Pneumatic Tube?
Pneumatic tubes (aka capsule pipelines or PTT) uses compressed air or vacuum to transport solid carriers through interconnected tubes. Unlike fluid pipelines, these systems move documents, lab samples or small parts swiftly and safely over short to medium distances.
How Pneumatic Tube Systems Work
- Pressure Generation: A blower (fan + motor) creates a pressure differential.
- Carrier Dispatch: At the sending station you insert your carrier, select the destination, and press “Send.”
- Airflow & Routing: The blower propels the carrier through the tubes. Intelligent diverters at junctions guide it along the correct path.
- Reception: The receiving station detects the carrier, depressurizes, and unlocks it for retrieval.
Major System Components
Component | Role | Best Practices |
---|---|---|
Carrier | Encapsulates items; cushions impact | Choose leak-proof materials for liquids |
Station | Dispatch & receive portals | Ensure user-friendly interfaces |
Diverter | Routes carriers at branch points | Test routing logic after installation |
Blower | Generates airflow | Match blower CFM to total tube length |
Pneumatic Tubing Types at A Glance
Material | Properties | Typical Applications |
---|---|---|
Polyurethane (PU) | Flexible, hydrolysis‑resistant, long service life | General automation, robotics |
Fluororesin (PTFE) | Exceptional corrosion resistance | Acids/bases, ultrapure water systems |
Polyolefin (TPH/TPS) | Clean‑room compatible, color‑coded | Medical, laboratory automation |
Spark‑Resistant Tubing | Flame‑retardant UL‑94 V‑0 outer layer | Welding booths, hot work environments |
Wear‑Resistant Tubing | High abrasion resistance | High‑cycle automation, tight‑bend piping |
Polyethylene Pneumatic Tubing | Lightweight, chemical‑resistant, cost‑effective | Food & beverage, light‑duty pneumatics |
Moisture Control Tubing | Diffuses water vapor to prevent condensation | Small cylinders, air‑operated valves |
The IDK series from SMC is a moisture-controlling tube. Condensation within a pneumatic system will result in operational failure and reduce the longevity of pneumatic equipment. The IDK prevents condensation in small cylinders, air grippers, and air-operated valves by diffusing water vapor from the piping before it condenses.
How to Choose the Right Tube Size
Selecting the correct ID (inner diameter) and OD (outer diameter) ensures proper airflow and carrier speed without excessive noise or wear.
Imperial Size | Metric Equivalent | Imperial Size | Metric Equivalent |
---|---|---|---|
⅛″ | 3.2 mm | ⅜″ | 12 mm |
5⁄32″ | 4 mm | ½″ | 16 mm |
3⁄16″ | 6 mm | — | — |
¼″ | 8 mm | — | — |
5⁄16″ | 10 mm | — | — |
Tip: Always consult your carrier manufacturer’s recommended ID clearance (usually +0.5 mm) to avoid jamming.
Installation & Maintenance Best Practices (2025)
- Pre‑Run Testing: Pressure‑test each tube segment at 1.5× operating pressure.
- Clean‑In‑Place (CIP): Flush lines quarterly if handling sensitive materials.
- Monitor Wear: Inspect abrasion‑prone bends every 6 months; replace before ID drops > 10 %.
- Vibration Control: Use foam‑lined clamps on long runs to dampen vibration and extend tube life.
- Digital Monitoring: Integrate flow & pressure sensors into your IoT platform for real‑time alerts.
FAQs
Q1. What’s the max recommended run‑length for a standard PU tube?
A: For 8 mm ID PU tube, keep straight‑line runs under 60 m; add booster blowers for longer distances.
Q2. Can I bend PU tubing by hand on the fly?
A: Small‑diameter PU (≤ 8 mm) can be hand‑bent; larger sizes require mandrels to avoid kinking.
Q3. How do I prevent moisture buildup?
A: Install inline moisture‑control tubing (e.g. SMC’s IDK series) upstream of sensitive valves and cylinders.
Partnering with SMC allows us to offer reliable pneumatic tube systems and expert guidance to meet the unique needs of our customers. If you have any further inquiries or require assistance with pneumatic tubes, contact us today.