Bottom Line Up Front: Upgrading to high-performance dust collector valves like SMC's new JSXFA and JSXF series can save industrial facilities thousands of dollars annually through reduced downtime, lower energy consumption, and extended filter life, often paying for themselves within months.
When most facility managers think about dust collection systems, they focus on the big-ticket items: the baghouse structure, the filters, and the fans. But there's a small component that can make or break your entire operation's profitability: your pulse valves. These seemingly simple devices are working behind the scenes, and when they fail or underperform, the financial ripple effects can be staggering.
The Real Cost of Valve Failures
Downtime: The Silent Profit Killer
Consider a steel smelting facility where a single valve failure leads to inadequate filter cleaning. As dust accumulates on filter bags, airflow decreases, forcing the system to work harder. Within hours, differential pressure alarms start triggering. By day two, production may need to slow down. By day three, you're looking at a complete shutdown for emergency maintenance.
Real-world impact: A mid-sized steel mill typically loses $50,000-$100,000 per day during unplanned dust collection downtime. If your traditional valves fail after 2-3 million cycles (industry standard), you're facing this scenario multiple times per year. SMC's new JSXFA and JSXF series, both engineered for 10+ million cycles, can extend this interval by 3-5 times.
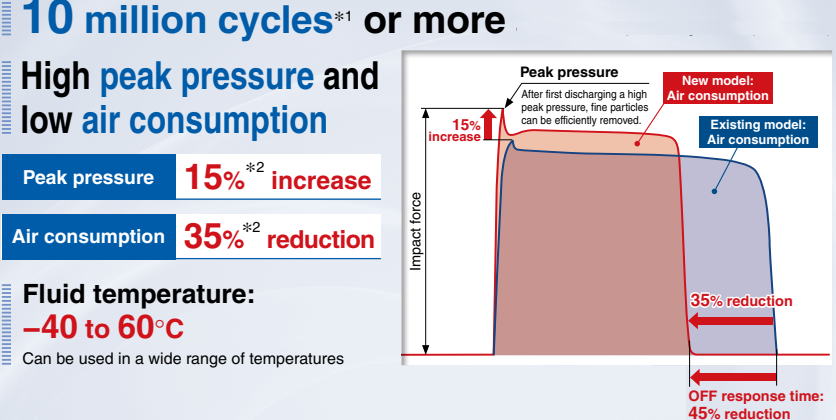
Energy Waste: Death by a Thousand Cuts
Here's where the math gets interesting. Traditional spring-loaded pulse valves often require higher operating pressures and longer pulse durations to achieve effective cleaning. Both SMC's JSXFA and JSXF series feature springless elastomer diaphragm designs that deliver 35% reduced air consumption while providing 15% increased peak pressure.
Let's crunch the numbers: A facility running 100 traditional valves at 6 bar pressure, pulsing 1,440 times daily, consumes approximately 2,500 cubic meters of compressed air per day. At $0.05 per cubic meter (typical industrial rate), that's $125 daily, or $45,625 annually just for pulse air.
With SMC's new JSXFA and JSXF valves delivering 35% air consumption reduction, the same facility saves $15,969 per year in compressed air costs alone. Over a 10-year valve lifecycle, that's nearly $160,000 in energy savings.
Industry-Specific Financial Impact
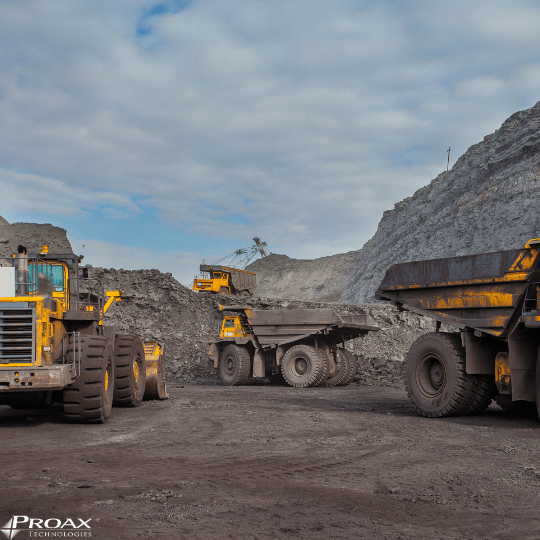
Mining Operations
In mining, dust collector downtime doesn't just stop production; it can trigger safety shutdowns across entire sections. Underground operations are particularly vulnerable, where a single pulse valve failure can cascade into evacuation procedures costing hundreds of thousands in lost production.
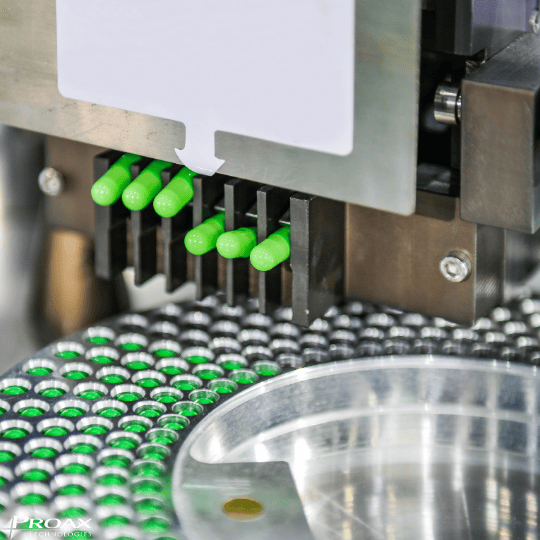
Pharmaceutical Manufacturing
For pharmaceutical facilities operating under strict FDA guidelines, filter integrity is critical. Poor pulse cleaning leads to premature filter replacement, but more importantly, it risks contamination events that can result in batch losses worth millions and regulatory complications.
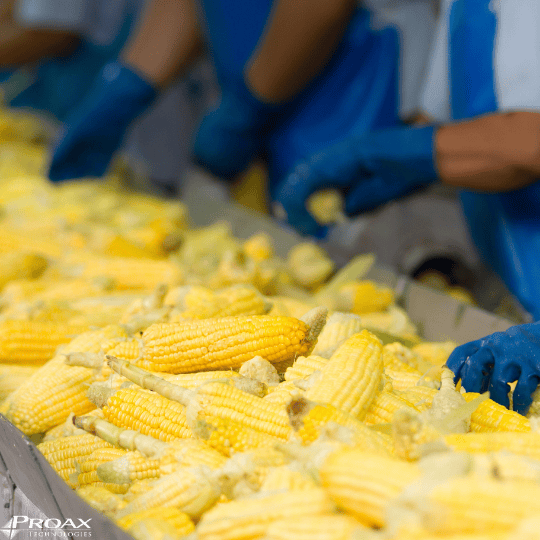
Food Processing
In grain handling and food processing, inadequate dust collection creates explosion risks. Both SMC's JSXFA series (ATEX Category 2) and JSXF series (ATEX Category 3) offer certified explosive atmosphere compliance, while their reliable performance reduces the risk of costly safety incidents.
The Technology Behind the Savings
Springless Innovation
Traditional pulse valves rely on springs that weaken over time, leading to inconsistent cleaning and eventual failure. Both SMC's JSXFA and JSXF series feature robust elastomer diaphragms that eliminate this failure point, creating more reliable sonic shock waves that effectively dislodge dust without the mechanical wear associated with spring mechanisms.
Integrated vs. Modular Design Options
The JSXFA series offers flexibility with solenoid or air-operated pilot valve actuation, making it ideal for retrofit applications or systems requiring specific control configurations. The JSXF series features an integrated solenoid design that simplifies installation and reduces potential failure points, perfect for new installations or complete system upgrades.

Faster Response, Better Cleaning
Both valve series deliver 45% faster response times, meaning shorter pulse durations achieve better cleaning results. This translates to:
- Reduced compressed air consumption
- Lower stress on filter media
- More consistent differential pressure
- Extended filter bag life
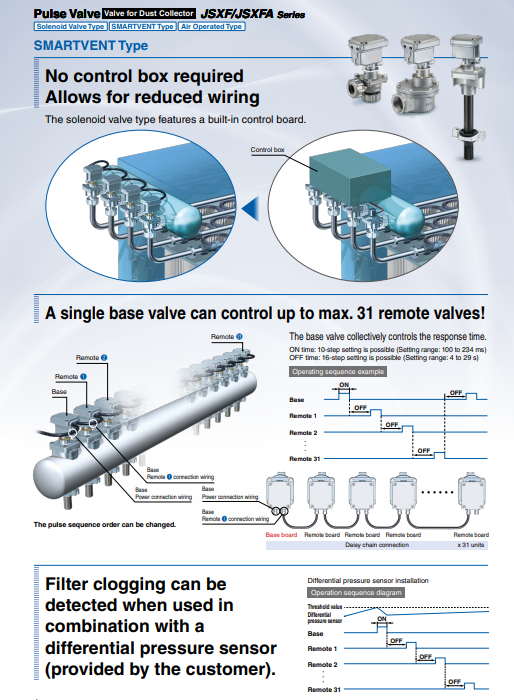
Smart Control Integration
The SMARTVENT control system can manage up to 32 pulse valves with precise timing control. This eliminates the inefficiencies of simple timer-based systems, optimizing cleaning cycles based on actual conditions rather than arbitrary schedules.
Calculating Your ROI
To determine if upgrading makes financial sense for your operation, consider these key metrics:
Annual Valve Maintenance Costs: Traditional valves requiring replacement every 2-3 years vs. SMC's JSXFA and JSXF valves lasting 5+ years based on cycle life.
Energy Consumption: Current compressed air costs for pulse cleaning vs. 35% reduction with SMC's new JSXFA and JSXF technology.
Filter Replacement Frequency: How often do you replace bags or cartridges due to incomplete cleaning vs. extended life with improved pulse effectiveness.
Downtime Incidents: Historical unplanned maintenance events related to dust collection vs. projected reduction with higher reliability valves.
Most facilities discover that SMC's new JSXFA and JSXF valves pay for themselves within 12-18 months through energy savings alone, with additional returns from reduced maintenance and extended component life.
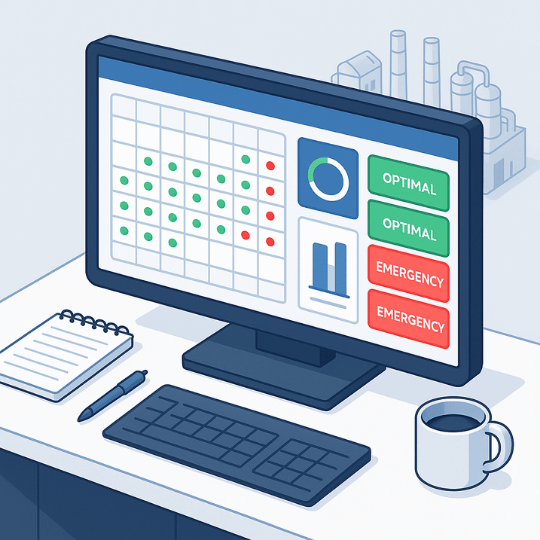
Beyond the Numbers: Operational Benefits
While the financial case is compelling, the operational advantages extend beyond pure cost savings:
- Predictable Maintenance: With 10+ million cycle life, you can schedule valve maintenance during planned outages rather than reacting to failures.
- Consistent Performance: Stable pulse pressure and timing mean your dust collection system performs reliably day after day.
- Simplified Inventory: Fewer valve types and longer service intervals reduce spare parts inventory requirements.
- Reduced Safety Risk: More reliable dust collection means fewer explosive dust accumulation incidents.
The Upgrade Decision
The question isn't whether high-performance pulse valves like SMC's JSXFA and JSXF series provide value; the financial case is clear. The question is whether you can afford to keep losing money on inefficient, failure-prone technology.
For facilities serious about operational efficiency and cost control, dust collector valve upgrades represent one of the highest-return investments available. With energy savings, reduced maintenance, and improved reliability, these small components deliver outsized impact on your bottom line.
Ready to calculate your specific savings potential?
Consider conducting an energy audit of your current dust collection system and compare it to the performance specifications of modern pulse valve technology. The numbers may surprise you, and your CFO will thank you.
As SMC's elite distributor, Proax offers expert consultation to help you determine the best valve solution for your specific application. Contact us to discuss your dust collection challenges and discover how upgrading to SMC's latest pulse valve technology can transform your operational efficiency.