A pneumatic actuator is a part of a device or machine that enables it to carry out physical movements. It achieves this by converting energy, often electrical, air, or hydraulic, into mechanical force. It is the component in a machine that enables movement. It can be compared to muscles in a body that enable energy to be converted to some form of motion like the movement of arms or legs, actuators work in a machine to perform a mechanical action. The actuator, like a muscle, receives a signal and it carries it enables the physical motion it is designed for. Some actuators return to rest in the absence of a signal, others require a different signal to return to rest state.
Actuators are present in almost every machine around us, from simple electronic access control systems, the vibrator on your mobile phone and household appliances to vehicles, industrial devices, and robots. In this post, we are going to discuss actuators for Industrial applications.
Types of Actuators Based on Energy Source
Hydraulic Actuators: Hydraulic actuators are suitable for high force applications as they can provide about 25 times more force than similarly sized pneumatic actuators. They operate at much higher pressures as well. They can also hold force and torque constant as hydraulic oil is much less compressible (about 10,000 times) than air.
A typical piston-type hydraulic actuator consists of a cylinder, a piston, a spring, a hydraulic supply and return line, and a stem. The piston slides vertically inside the cylinder and separates the cylinder into two chambers. The upper chamber contains the spring and the lower chamber contains hydraulic oil (this could be reversed if we want the force on the extend motion instead of the retract motion). The hydraulic supply and return line is connected to the lower chamber and allows hydraulic fluid to flow to and from the lower chamber of the actuator.
Initially, with no hydraulic fluid pressure, the spring force holds the valve in the closed position. As fluid enters the lower chamber, pressure in the chamber increases. This pressure results in a force on the bottom of the piston opposite to the force caused by the spring. When the hydraulic force is greater than the spring force, the piston begins to move upward, the spring compresses, and the valve begins to open. As the hydraulic pressure increases, the valve continues to open. Conversely, as hydraulic oil is drained from the cylinder, the hydraulic force becomes less than the spring force, the piston moves downward, and the valve closes. By regulating amount of oil supplied or drained from the actuator, the valve can be positioned between fully open and fully closed.
Hydraulic Actuators leak fluid, which results in less efficiency and cleanliness problems. They also require more complementary parts like a fluid reservoir, motor, pump and noise reduction equipment.
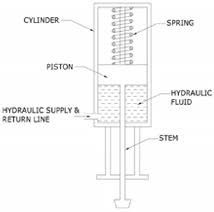
Pneumatic Actuators: Pneumatic actuators are one of the most popular engineering devices, and the most common type of actuator because they are highly reliable, efficient, and safe sources of motion control. They convert energy, typically in the form of compressed air, into mechanical motion. Pneumatic actuators are recognised by several different names including pneumatic cylinders, air cylinders, and air actuators.
Pneumatic actuators have a similar operating principle to hydraulic actuators. Consisting of a piston, cylinder, and valves or ports, a pneumatic actuator can convert energy into linear or rotary mechanical motions. This is dependent on whether the application is using a pneumatic rotary actuator or a linear actuator. The “Double Acting” actuator has two chambers that can be filled with air to enable motion in either direction, while the “Single Acting” configuration has a spring for motion in on direction and a chamber to be filled with compress air for motion in the other.
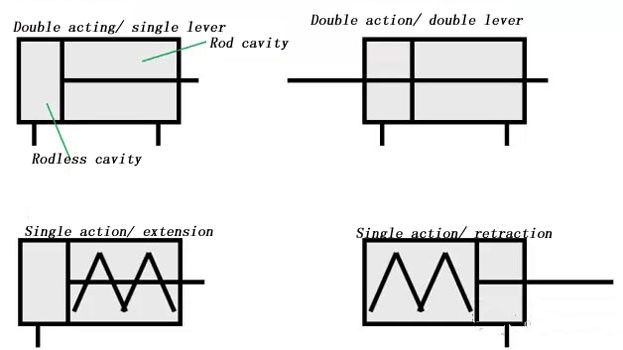
The fact that they do not require ignition or electricity makes these devices highly sought after where parking and combustion are not tolerated. This is because a pneumatic actuator can store compressed air and use it again efficiently without the risk of fire. Pneumatic actuators are also extremely durable and can, therefore, reduce the costs required to maintain its performance. Less maintenance means a longer product lifecycle and therefore greater output.
Electric Actuators: Electric actuators generate motion using an electric motor. The motor rotates a lead screw or a gear train, which moves a rod or arm back and forth. Applications requiring precise control and positioning or multiple stops in between full stroke extension and retraction, frequently employ electric actuators.
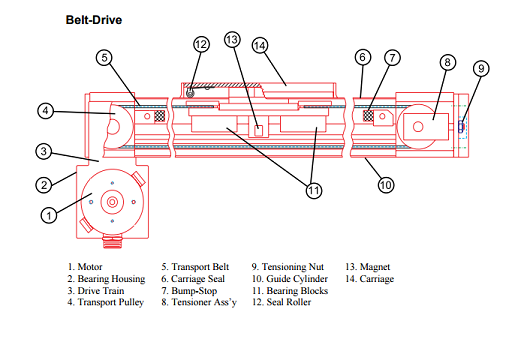
SMC Electric Actuators are cutting-edge automation tools Equipped with incremental encoders designed for exceptional performance and reliability.
Actuators Based on Motion Type
Linear Actuators: Basic linear air cylinders are used to provide straight-line, in/out linear movement for a variety of applications. Available as single acting (spring extend or spring return actuators) and double acting styles with single rod or double rod configurations, non-rotating, and precision non-rotating models.
Actuator body styles include crimped, round, or tie rod. Single acting air cylinders develop thrust in one direction and have spring return mechanism, which lowers air consumption compared with the equivalent size of double acting air cylinders. Using a double acting air cylinder, air pressure may be alternately applied to provide force in both directions.
Linear actuators can also have guide rods mounted parallel to the piston rod to provide stable, non-rotating, high side load performance. These are referred to as guided actuators.
Rotary Actuators: Rotary actuators provide rotational motion as opposed to linear motion. They are available with arc lengths of 90°, 180°, 190°, 270°, or even 360° depending on the configuration and method of actuation.
Grippers: Grippers are used for pick and place applications. They are available in many different configurations, including as rotary grippers, two, three and four finger parallel styles that are ideal for gripping and centering, a wide opening parallel model pneumatic gripper, designed to accommodate many different sized parts, a heavy duty style, suitable for a wide range of applications.
Clamps: Clamp cylinders are used for holding a workpiece in place while work is being done. Most clamp cylinders are designed for weld spatter resistance for long life.
As an elite distributor of SMC actuators, Proax Technologies is uniquely positioned to help guide you through the world of actuators. With our deep product knowledge and commitment to customer service, we're your trusted partner in automation solutions.
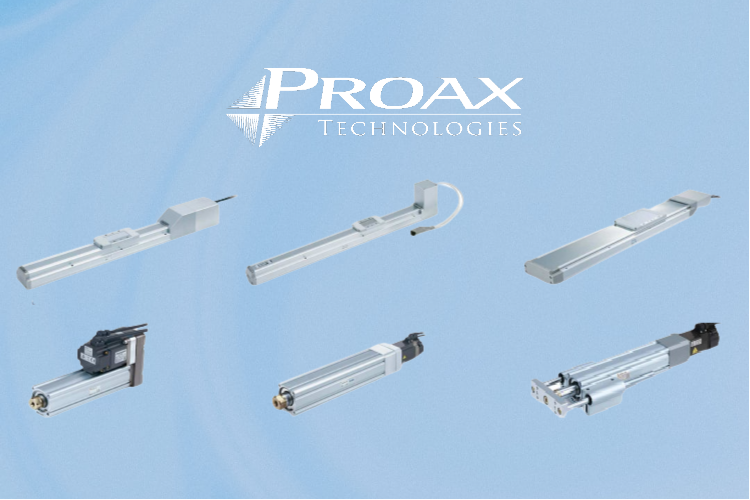
Contact us today to discover how our team can help you select the right actuator for your application, maximize efficiency, and push the boundaries of what's possible.