In the world of pneumatic systems, ensuring machine safety is paramount. Locking cylinders play a critical role in achieving this by providing reliable stopping and holding mechanisms. Whether it's for clamping during welding or maintaining a safety zone during repairs, these cylinders are indispensable.
What is A Pneumatic Cylinder Lock?
Pneumatic locking cylinders come in two main types: locking at extension or retraction and braking for mid-stroke positioning. Both can be activated by changes in air pressure, making them versatile tools for various industrial applications. However, to maximize their effectiveness and safety, it's crucial to follow best practices when installing and using these components.
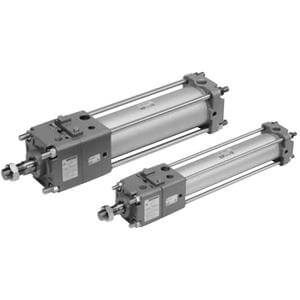
Best Practices for Using Locking Cylinders
1. Proper Installation
- Ensure correct alignment and secure mounting to prevent misalignment and potential failures.
- Verify compatibility with existing pneumatic systems and applications.
2. Regular Maintenance
- Conduct scheduled inspections and servicing to maintain optimal performance.
- Follow cleaning and lubrication guidelines to reduce wear and tear.
- Identify and address signs of wear promptly to avoid operational issues.
3. Selecting the Right Type
- Choose between mechanical and pneumatic locking cylinders based on the specific application requirements.
- Consider load capacity, environmental conditions, and the nature of the tasks (e.g., welding, drilling) when selecting locking cylinders.
4. Integration with Pneumatic Systems
- Use solenoid valves and control systems to connect and manage the locking cylinders effectively.
- Design pneumatic systems with appropriate flow controls and pressure regulators to ensure stability and precision.
5. Safety Protocols
- Establish clear emergency stopping procedures and ensure all operators are trained.
- Comply with industry safety standards and regulations to enhance overall safety.
6. Load Management
- Employ techniques for maintaining position under varying load conditions, preventing drift and unintended movements.
- Implement pressure regulators and flow controls to balance air pressure within the system.
Proax, with 13 locations across Canada, has helped customers in various industries nationwide integrate pneumatic locking cylinders. For example, an automotive manufacturer enhanced welding precision and safety on their assembly line with our SMC cylinders. In the food and beverage sector, we improved packaging machine reliability and reduced downtime. In aerospace, SMC locking cylinders increased accuracy and safety during drilling and assembly processes.
SMC Locking Cylinders
Proax, an authorized distributor of SMC, offers a range of SMC locking cylinders, which lock at any desired stroke position to prevent drops. These cylinders are ideal for emergency stops or intermediate stops. The locking position can be adjusted according to the external stopper position and the thickness of the clamped work-piece.
- CLQ Series: Compact locking cylinder suitable for applications with limited space.
- CLQ Series: CLQ offers drop prevention when the pressure of air source is decreased or the residual pressure is released. The CLQ has a low profile design, with a compact lock unit.
- CNA2: Features a built-in air cushion and a rod lock mechanism, ideal for vertical loads.
- CLG1: High-precision locking cylinder with integrated guide rods for stability and precision.
and you can visit more pneumatic locking cylinders here.
For more information on how to integrate locking cylinders into your industrial systems, contact us at Proax today. Our experts are ready to help you enhance your machine safety and operational efficiency.