Choosing the right electrical enclosure for your industrial project can feel overwhelming with so many options available. But get it right, and you'll safeguard your equipment while ensuring reliable operation for years to come. Get it wrong, and you might face premature equipment failure, safety hazards, or costly replacements down the line. Whether you're planning a new installation or upgrading your current setup, taking time to understand what makes an enclosure right for your specific needs pays dividends in both performance and peace of mind.
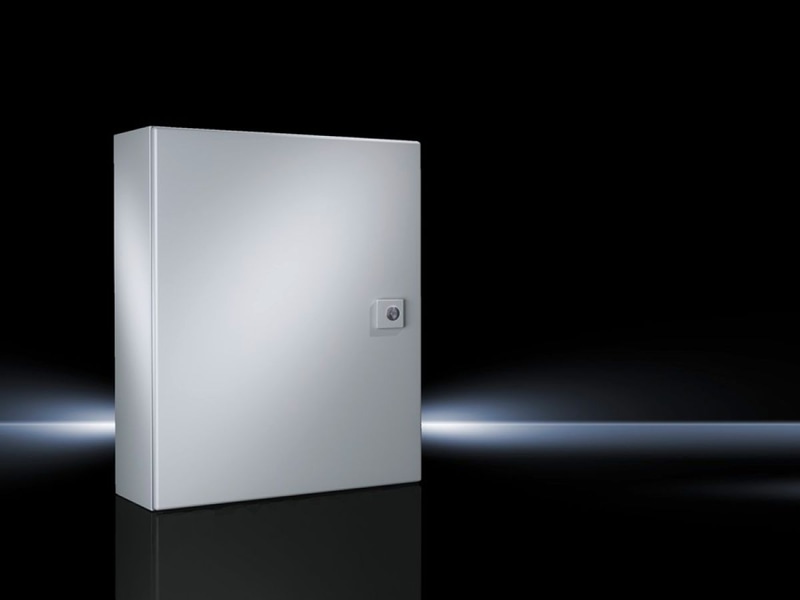
Why Enclosure Selection Matters
The proper electrical enclosure serves as the first line of defense for your equipment against environmental hazards, unauthorized access, and potential safety risks. A well-chosen enclosure not only protects your investment but also:
- Ensures compliance with industry regulations and safety standards
- Prevents unexpected downtime due to equipment failure
- Extends the service life of electrical components
- Provides appropriate access for maintenance while maintaining security
- Accommodates future system expansion and modifications
Let's explore the essential factors you need to consider when selecting an electrical enclosure for your specific industrial application.
Key Factors in Selecting the Right Electrical Enclosure
1. Environmental Conditions Assessment
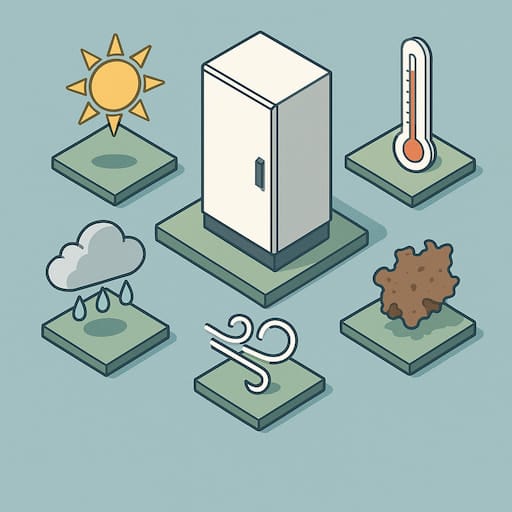
The environment where your enclosure will be installed should be your primary consideration. Different industrial settings present unique challenges:
- Dust and Particulates: Manufacturing facilities often generate airborne particles that can damage unprotected electrical components
- Moisture Exposure: Processing plants, outdoor installations, or washdown areas require enhanced protection against water ingress
- Chemical Presence: Industries handling corrosive substances need specially designed enclosures to prevent deterioration
- Temperature Extremes: Consider both ambient temperature ranges and heat generated by enclosed equipment
- Mechanical Impacts: High-traffic areas or locations with moving equipment may require impact-resistant enclosures
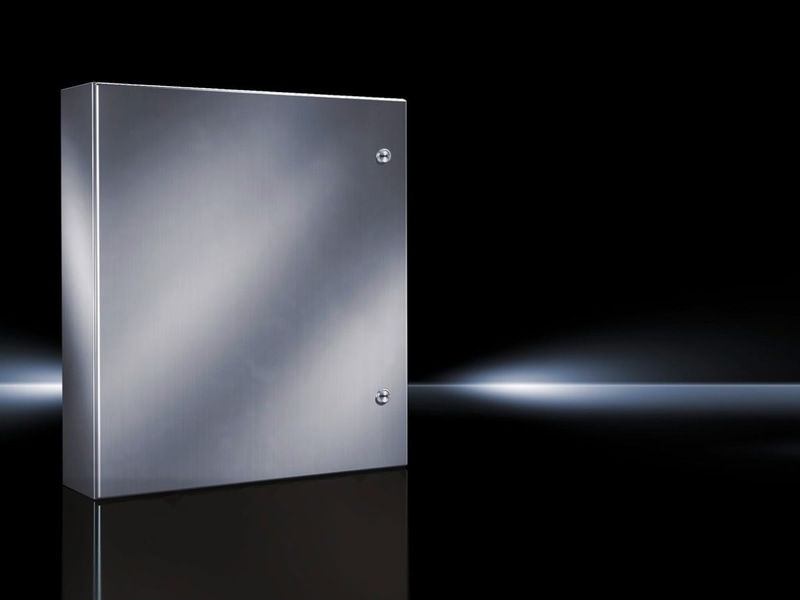
For particularly harsh environments like food processing or chemical plants, specialized solutions such as stainless steel enclosures or hygienic design enclosures provide superior protection against corrosion and facilitate thorough cleaning procedures.
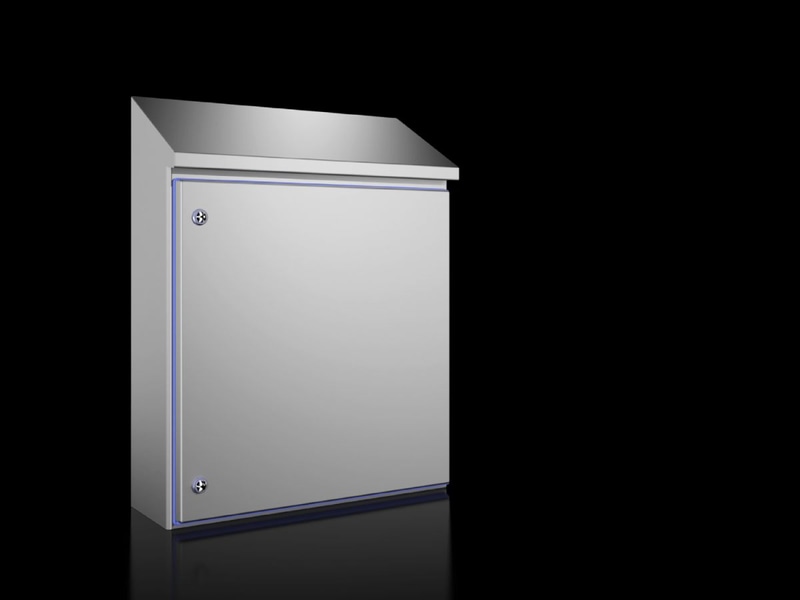
If your installation will be exposed to the elements, outdoor housings offer the necessary protection against UV radiation, precipitation, and temperature fluctuations.
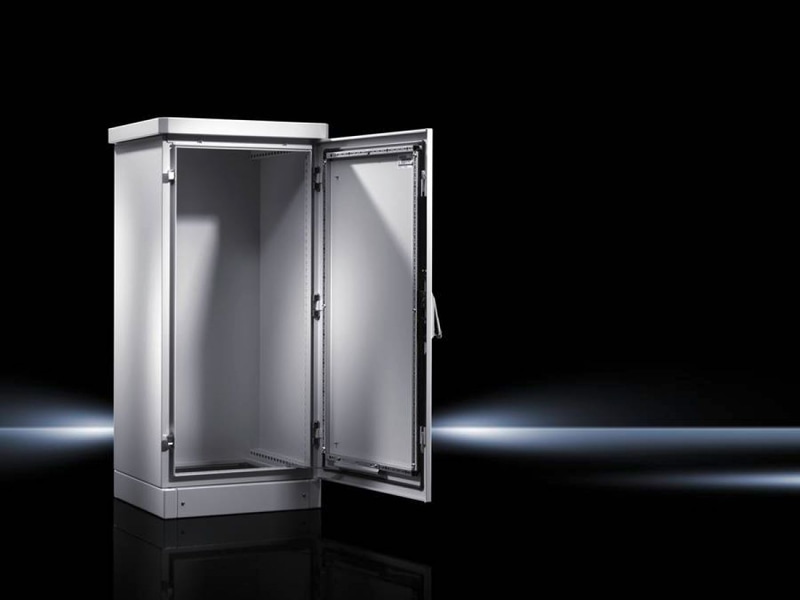
2. Protection Ratings: Understanding NEMA and IP Classifications
Protection ratings provide standardized measures of an enclosure's ability to resist environmental factors. In North America, NEMA (National Electrical Manufacturers Association) ratings are widely used, while IP (Ingress Protection) ratings are internationally recognized.
NEMA Ratings at a Glance
NEMA Rating | Protection Level | Typical Applications |
---|---|---|
NEMA 1 | Indoor, basic protection | General purpose indoor environments |
NEMA 3R | Weather-resistant | Outdoor installations with rain, sleet exposure |
NEMA 4 | Watertight | Locations with water spray, outdoor installations |
NEMA 4X | Watertight, corrosion-resistant | Corrosive environments, food processing |
NEMA 12 | Dust-tight, drip-proof | Industrial environments with dust, oil |
3. Material Selection for Durability and Performance
The enclosure material directly impacts its durability, weight, appearance, and protective capabilities:
Mild Steel: Economical and suitable for indoor applications, but requires proper finishing to prevent corrosion
Stainless Steel: Excellent for corrosive environments, food processing, and pharmaceutical applications due to superior resistance and cleanability
Aluminum: Lightweight, naturally corrosion-resistant, and offers good heat dissipation
Fiberglass/Polyester: Non-conductive, lightweight, and highly resistant to chemicals and corrosion
Polycarbonate: Impact-resistant, lightweight, and suitable for indoor and some outdoor applications
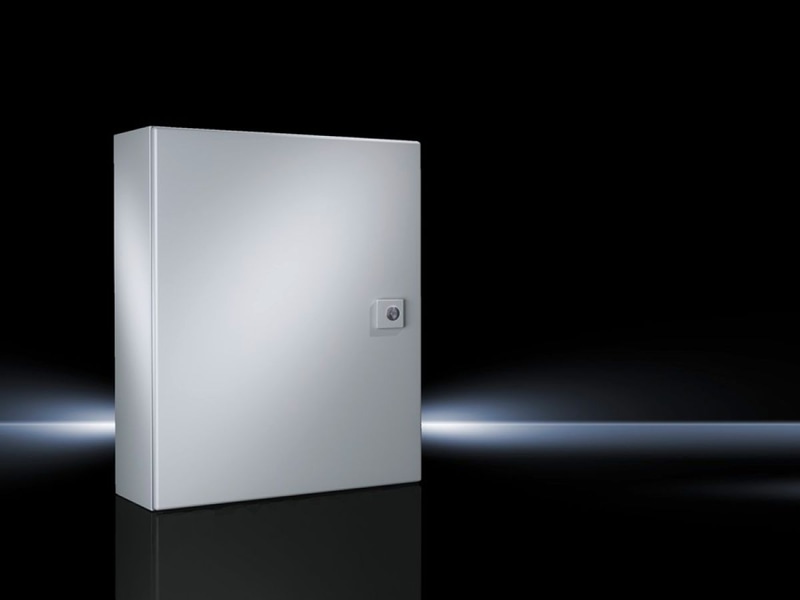
Your material choice should align with environmental conditions, budget considerations, and specific industry requirements. For instance, Rittal's wall-mounted enclosures are available in various materials to suit different industrial environments.
4. Size and Space Planning
Proper sizing ensures adequate space for components, wiring, and potential future expansion:
- Allow at least 30% extra space beyond your current requirements for future additions
- Consider clearance for heat dissipation around components
- Account for cable routing and bend radius requirements
- Evaluate accessibility requirements for maintenance and troubleshooting
- Factor in physical space constraints at the installation location
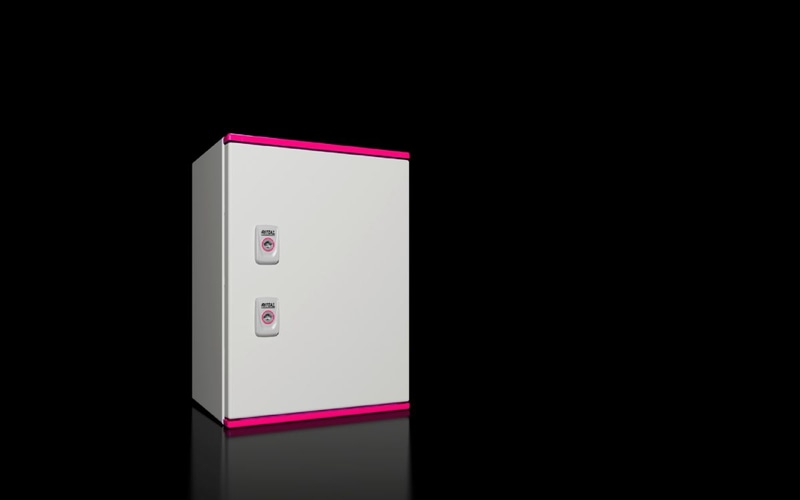
Compact enclosures provide efficient solutions for space-constrained applications, while modular and freestanding enclosures offer greater flexibility for larger systems or those requiring future expansion.
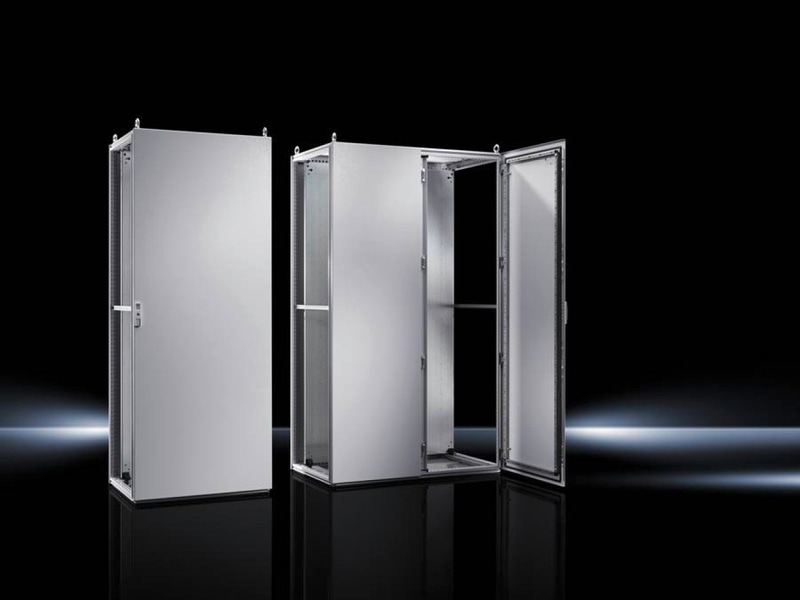
5. Access and Security Considerations
The method of access to your enclosure should balance operational needs with security requirements:
- Regular Access: Quick-release latches or simple key locks for frequently accessed equipment
- Limited Access: More sophisticated locking mechanisms for critical systems or high-voltage equipment
- Special Requirements: Tamper-resistant designs for public areas or padlockable options for lockout/tagout procedures
Disconnect enclosures provide safety features that facilitate proper lockout/tagout procedures for maintenance operations.
6. Mounting Options and Installation Requirements
Select mounting styles that accommodate your specific installation environment:
- Wall-mounted industrial enclosures: Ideal for control panels, instrumentation, and smaller equipment installations
- Junction & terminal boxes: Perfect for cable terminations and wiring connections
- Modular and freestanding enclosures: Suitable for large control systems, motor starters, and expandable installations
- Network and server rack enclosures: Specialized solutions for IT and networking equipment
The mounting style affects not only installation but also accessibility, space utilization, and equipment protection.
7. Climate Control Requirements
Heat management is crucial for maintaining optimal operating conditions for electrical components:
- Calculate heat loads from equipment and environmental factors
- Consider passive cooling options like ventilation for lower heat loads
- For higher heat loads or sensitive electronics, active climate control solutions like fans, air conditioners, or heat exchangers may be necessary
Proper climate control prevents premature component failure and ensures system reliability.
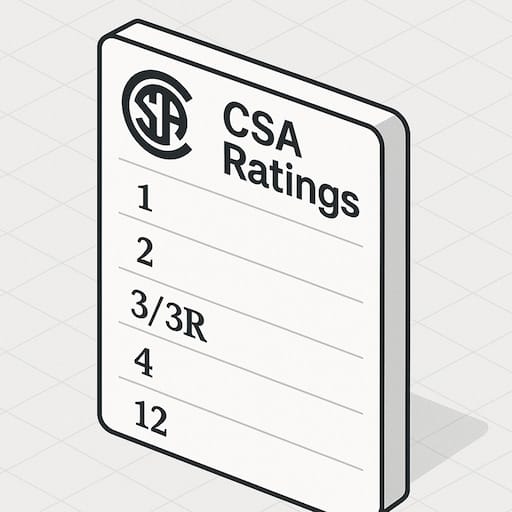
8. Canadian Standards and Certifications
For installations in Canada, compliance with specific standards is essential:
CSA Ratings (Canadian Standards Association)
Canadian electrical installations must comply with CSA standards referenced in the Canadian Electrical Code (CEC), Part I (CSA C22.1).
CSA Type | Protection Level | Typical Use |
---|---|---|
1 | General purpose, indoor | Basic protection against contact |
2 | Drip-tight, indoor | Areas with condensation (e.g., laundries) |
3/3R | Weather-resistant, outdoor | Rain, sleet, snow, wind-blown dust |
4 | Watertight, dust-tight | Hosedown, very wet environments |
4X | Same as 4, plus corrosion resistance | Food processing, dairies, refineries |
12 | Drip and splash protection | Light splashes, industrial environments |
Always look for CSA or cUL certification on enclosures for use in Canadian installations to ensure regulatory compliance and safety.
Selection Checklist for Your Industrial Electrical Enclosure
Before making your final decision, use this checklist to ensure you've considered all critical factors:
- □ Identified all environmental hazards (dust, water, chemicals, temperature, impact)
- □ Determined appropriate NEMA/IP/CSA protection ratings
- □ Selected suitable material for durability and environmental resistance
- □ Calculated adequate size with room for future expansion
- □ Considered appropriate access and security features
- □ Evaluated mounting and installation requirements
- □ Assessed climate control needs
- □ Verified required certifications and regulatory compliance
Conclusion
Selecting the right electrical enclosure for your industrial application requires careful consideration of multiple factors. By thoroughly evaluating your specific needs and environmental conditions, you can choose an enclosure that provides optimal protection, accessibility, and longevity for your electrical equipment.
At Proax, we offer a comprehensive range of electrical enclosure solutions to meet diverse industrial requirements. As an authorized Rittal distributor, we provide access to industry-leading enclosure solutions backed by exceptional technical support. Our product specialists can help you navigate the selection process and find the perfect enclosure for your application.
Contact Proax today to discuss your electrical enclosure needs and discover how our solutions can enhance the safety and reliability of your industrial electrical systems.